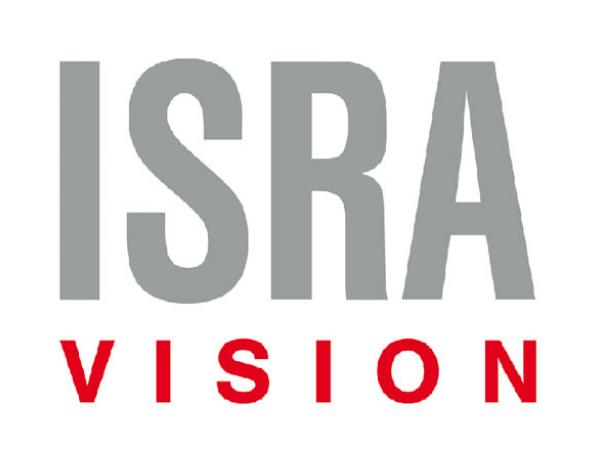
Date: 19 April 2016
FLABEG FE, world market leader in the glass processing industry, was looking for an inspection system for 100% online measurement of their produced mirrors and new products. The company wanted the in-process control to allow precise and repeatable measurement within the normal cycle rate, and to enable a fast and direct reaction to any defects. FLABEG found its solution in the form of ISRA VISION's FORMSCAN – a system for contactless inline 3D shape measurement for glass with multidimensional bending.
The new ISRA VISION technology measures online the bending precision of the produced solar glasses, as soon as they leave the oven. Because the products are assessed directly at the bending oven, the operator can react to and counteract any defects extremely quick. “We chose ISRA not only because the solution was the best value for the money, but also we were aiming at the chance to correct defects immediately,” explains Dipl-Ing Andreas Seidl, Head of Process Technology at FLABEG. ISRA VISION is the only company in the world to offer such a comprehensive product range for the optical surface inspection of glass. The inspection systems are deployed at every stage of the process, from float glass production to the final quality control. The data gathered from the inspection systems also serves as a basis for process optimization.
At FLABEG, FORMSCAN Solar II – just one of a series of successful, fully automated FORMSCAN systems – is implemented for contactless 3D shape measurement of all kinds of curved, multidimensional glass components. In addition to solar mirrors, the systems can also be applied for measuring curved architectural glass, car windows, glass lenses, glass for electronic applications, mirrors for astronomical telescopes, hobs and much more in real time.
Outstanding perfection for glass inspection
The FORMSCAN inline measuring system typically takes advantage of more than 1,000,000 measuring points per square meter, enabling accuracies down to tenths of a millimeter. For its 3D measurement, ISRA uses the unique, patented stereo deflectometry process for most precise results. Thanks to valuable components, the system is very sturdy and requires low maintenance efforts. The inspection system allows 100% of the solar parabolic mirrors produced to be measured immediately after the bending process. This benefits both, the manufacturers and their customers. Every mirror delivered has its own measured value, which ensures that all the mirrors display the values specified by the customer. This is the only way to guarantee 100% functionality of all the mirrors produced for the highly competitive solar industry.
“Just like the previously used ISRA measuring system, the system is one of the key components of the bending process alongside the oven and the grinding system, so it is absolutely essential,” says the Head of Process Technology. “Without a measuring system that works correctly, there is no way to check the bending process and therefore the product quality.” The new ISRA inspection system also allows the measurement to take place in a horizontal position – one of the reasons FLABEG chose it. Until now, the mirrors were measured vertically and the values then converted for horizontal measurement.
Excellent classification performance
“As well as the high level of repeat accuracy across the entire surface of a still mirror, the high level of concordance with the current standard measuring system QDec is very impressive,” says Dipl.-Ing. Alexander Achatz from Quality Assurance. “When comparing the individual values from the measuring points, more than 90% of the values are within the standard deviation.” “The measuring system is also very effective at differentiating between the quality levels of individual mirrors,” adds Seidl. “Any measuring system with a value of less than 10% R&R (repeatability and reproducibility) is considered excellent.”
FLABEG FE designed and implemented the construction for the support of the measuring object, supporting the position and shape of the mirror used in the ISRA measuring system in the best possible way. Very precise and quick to adjust to different mirror types, the construction guarantees that the solar mirrors rest on four points in exactly the same way as they would on the solar field.
Support for process optimization
One of the functions of the new ISRA measuring system is the automatically sorting of the glass, based on preset limit values: The system classifies the mirrors, it measures into the quality categories ‘OK’ and ‘Not OK’ based on predefined limit values and the current average value for the project in question. Products showing insufficient quality are weeded out before they enter further processing. The 100% measurement also allows the bending process to be monitored more effectively. Seidl is certain that “the anticipated rejection figures can be reduced even further in the long term.”
Summary
With the new inspection system, 100% of the produced solar mirrors are measured precisely across their entire surface. FORMSCAN thus enables full-field measurement with 100% documented quality and a fast reaction time for process adjustments. The result is a totally new level of quality. Complete measurement of the products and analysis in the evaluation software come together to provide a systematic optimization of production lines. The high availability of the inspection system is also very impressive. The complete lack of wearing parts in the system automatically reduces maintenance costs.
For the introduction of the new measuring system, ISRA and the customer organized and coordinated the planning, arrangement and execution flawlessly. The finished system, accepted by FLABEG, meets all requirements specified. “The collaboration between the project teams worked efficiently and was extremely constructive, allowing the system performance to be constantly increased even during the project,” concludes Seidl happily.
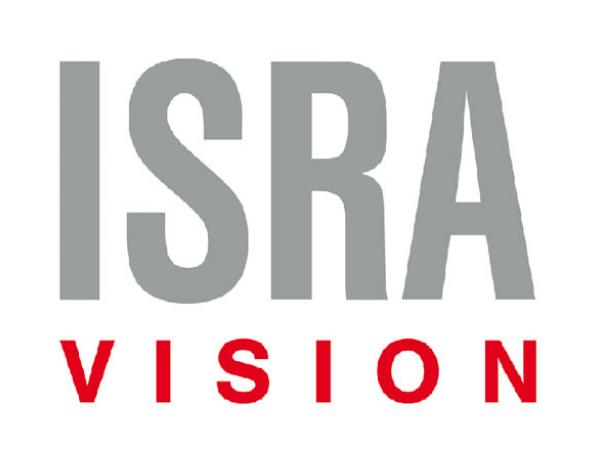

Add new comment