Industriestraße 21
Beverungen 37688
Germany
HEGLA GmbH&Co. KG
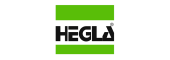
Find us on:
HEGLA develops, produces and sells machinery, plants and equipment for flat glass processing and refinement, storage and logistic systems for glass and windows, as well as superstructures for lorries and transporters. Expert advice and comprehensive maintenance services round off our portfolio.
Products or Machinery
Glass storage and conveyor systems
Efficient working practices start in the glass store. Only if the maintenance of stocks is properly organised can access times be reduced and spare production capacity released. HEGLA’s space-saving automatic compact storage system means that available space in the raw glass store is used in the optimum way and the number of glass products can be increased without the need for more space.
Automatic conveyor systems link the glass store with the cutting shop. Whether the glass store consists of fixed frames, automatic compact stores or a combination of the two, a HEGLA portal conveyor supplies one or more cutting lines continuously with glass. The rotatable portal conveyor can select various different glass formats from each storage area and place them at the front without the need for additional operator intervention.
Galactic – Float glass cutting plant
The Galactic float glass cutting plant with electromagnetic linear drives has a highly dynamic movement with acceleration of 15 m/s². In conjunction with the high resolution measurement system, these linear drives – without mechanical gears – set benchmarks in precision. Furthermore, the contact-free linear drives permanently minimise wear and tear.
Automatic breaking plants for float glass
Hegla’s automatic breaking plants are designed for automatic breaking of glass sheet sections in an X and Y direction. Specially equipped breaking strips and hold-down devices guarantee that breaking quality remains constant. To remove narrow residual strips from the production process, the plant can be equipped with a tilting frame, through which the residual strips can be ejected beneath the plant. By integrating the Tandem-ReMaster, residual sheets can be transferred in and out automatically, without loss of cycle time. In combination with the glass sheet rotation station HEGLA-TraCon, automatic X-Y breakage systems can also be designed with only one product direction (X direction).
ReMaster – Dynamic residual sheet store
The dynamic intermediate storage system ReMaster represents a space-saving residual sheet storage system which can be installed above the cutting plant for the dynamic intermediate storage of residual sheets. Residual sheets, in particular of expensive special glasses, can be taken into account again by the optimisation system, without operator intervention. Damage to the glass is therefore excluded, and optimum use of materials guaranteed even when there is a wide variety of products and a continuous flow of glass.
Laminated glass separation technique
The flexible and precise cutting of composite safety glass is also one of the strengths of the HEGLA Group.
Composite safety glass can be cut precisely and without misalignment on HEGLA’s laminated glass cutting systems; two special cutting heads running exactly above one another for this purpose. A separation process optimised to the types of glass guarantees the constant high quality of cutting results, with the shortest cycle times. With the automatic laminated glass cutting lines, the excess length of foil can be automatically removed during inward transfer. This patented foil-peeling device brings additional gains in terms of precision and process reliability during subsequent processing stages.
SortJet – sorting systems
The SortJet systems make a major contribution to reducing material costs and improving production flow within insulating glass production. The SortJet systems takes the glass from the chaotic breaking sequence, which is optimised for cutting, into the necessary production or despatch sequence. The sheets required for insulating glass production are brought together in the SortJet and, depending on the degree of automation, the systems can be delivered with automatic glass surface change, automatic stacking or a direct connection for insulating glass lines.
De-stacking and transport technology for coating plants
Coating plants and cutting plants require rapid access to various sizes of glass. The HEGLA stackers are designed for industrial use, especially for coating plants and mirror application lines. Very short cycle times combined with the highest level of precision are what distinguish these HEGLA products.
From the gantry solution up to and including robotics, from the belt dimension to small format, HEGLA’s stacking technology will provide the perfect solution for your application.
Photovoltaics – Plants and production logistics
Further new product developments have been undertaken in the area of photovoltaic panels. Here the focus is for the most part on plant and production logistics. In particular the rapid supply of solar process lines, obtained by preference with the extremely dynamic, rail-guided HEGLA coating module. The programme is completed by robot technology for stacking and outward transfer.
Company Background / History
For 35 years HEGLA has played an important role in cutting and processing flat glass. Over this time the name of HEGLA has stood not only for outstanding quality, but also for continuous development and product innovation. Our strength is the development of tailored solutions for our customers worldwide in the flat glass and solar industry.
Innovative strength, the use of the most modern techniques, high quality level and competence together with committed application of our around 500 employees have madeus into a leading worldwide supplier. HEGLA develops, produces and sells solutions for the storage, processing and transport of flat glass – from high tech cutting systems with coating and breaking systems up to automatic sorting installations. In many areas we are technology and market leaders with an international platform.
Customer satisfaction is our central focus. This means that as innovative machine builders we have long since ceased to be simply manufacturers; above all we provide services for our customers. Requirements are established on site and solution proposals are worked out by our engineers and sales staff.
Our customers include:
- Basic glass manufacturers
- Glass coating firms
- Manufacturers of insulating glass
- Flat glass wholesalers
- Flat glass refining companies
- The photovoltaic and solar panel industry
- The car industry
Product areas/ product divisions in the HEGLA Group:
- Mechanical and plant engineering
- Glass storage and preparation systems
- Conveyor systems
- Float glass cutting technology
- Laminated glass separation technology
- Dynamic storage system for residual sheets
- Automatic breaking systems
- SortJet sorting systems
- De-stacking and transport technology for coating plants / mirror coating lines
- Plant and production logistics for photovoltaic panel production
- Storage and logistics systems
This range of supply is enhanced by the highly competent After Sales Service provided by our subsidiary HEGLA GmbH & Co. KG, Wartung und Service (Maintenance and Service).
Maintenance and Service
For HEGLA, customer service does not end with sales and assembly. Our own independent subsidiary HEGLA Wartung und Service is your ideal “After Sales” partner. Only qualified, quick and reliable service gives our worldwide customers the certainty they require. The certainty that machinery and installations are guaranteed ready to operate, and will function smoothly. The certainty that down-times will be reduced to a minimum and operating cost will remain inside the budget forecast. Our service network today is worldwide and extends to cover all time zones.
The most modern techniques such as remote maintenance (HEGLA TeleDiagnostics) via the internet and individual service packages provide security and save costs.
Quality policy
Nothing is so good that it cannot be improved. Striving constantly for a better solution and “Quality in everything we do” are the guiding principles to which our employees work. Experienced engineers, technicians and specialist workers are the guarantors of a constantly maintained high quality levels. Quality has to be developed and produced, not just checked!
3D design, computer-assisted production planning and control, efficient materials management, economically sound production processes and close co-operation with qualified suppliers are the pillars on which this is built.
We have been certified to the level of DIN EN ISO 9001:2008 since 1995.