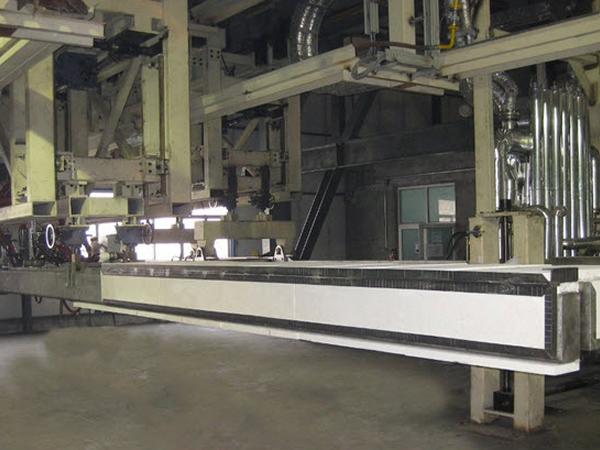
Date: 21 February 2017
Magnetron sputtering is the most common PVD process. Sputtered coatings are generally referred to as “soft-coat” because they are “painted on” by ionized metals directed at the glass.
CVD coatings are referred to as “hard-coat” because they are burned onto the glass and become part of the structure. These coatings can be harder than the glass itself and boost chemical resistance.
Both types of coating offer advantages and disadvantages. When evaluating the best option for a glass manufacturing facility, coating performance and ease of fabrication are important factors.
Magnetron Sputtered Technology
Sputtered coatings are applied independently of the float glass manufacturing process (“off-line”). Thin films are formed by accelerating high energy ions from targets toward the glass surface at low temperatures.
The ions bombard the glass surface forming uniform thin layers. The bond is weak, causing a “soft coating” that is more easily scratched or damaged and chemically fragile.
Commercial sputtered coatings are applied in a vacuum chamber and typically consist of 6-12 layers of thin metallic and oxide coatings. Silver is the active layer for “Low E” (low emissivity) sputtered coatings.
Remaining layers include barriers, color modification oxide layers, and sacrificial metal layers. Sputter manufactures use these additional layers to offer more products than pyrolytic producers offer.
Offline sputtered soft-coating offers a few benefits:
- Sputtering can be done by companies not involved in glass production.
- Sputtering is a well-established process with a broad range of target materials.
- Short delivery times are possible with less inventory per product.
- Sputtered coatings can offer better properties for some applications.
Many companies embrace sputter coating for the advantages listed above. Glass distributors only coating choice is to install sputter systems, which accounts for their popularity. However, glass manufacturers have other options and should consider the disadvantages of sputter coating listed below:
- Capital costs are higher for sputtering equipment relative to production capacity.
- Manufacturing costs are high due to materials, energy, maintenance, and depreciation (often 2 to 3 times the price of CVD coatings), resulting in low margins.
- Production yields decline as more layers are deposited.
- Sputtered coatings are soft and are damaged more easily during normal handling and fabrication.
- Sputtered coatings are sensitive to moisture requiring sealed bags with desiccant.
- Shelf life is limited in sealed packaging, but is further reduced after packaging is opened.
- Sputtered coatings have weak adhesion which can cause sealant failures in insulated glass units. Edge deletion of sputtered coatings is recommended which adds manufacturing costs. Sputtered coatings that “don’t require edge deletion” can experience rapid seal failure due to certain detergents and brick washes.
- Sputtered coatings cannot typically be used with single pane applications.
- Tempering soft coat requires unusual skill, and usually results in increased tempering losses.
Pyrolytic CVD Technology
Chemical Vapor Deposition (CVD) can produce a variety of aesthetic and functional coatings. Chemical vapors are brought to the hot glass surface with specialized coaters during glass manufacturing.
The vapors react with the hot glass (600°C to 700°C) and form a covalent bond. This results in a hard and robust coating that enhances the strength and stain resistance of the glass.
Fragile sputtered soft-coatings can be accidently wiped off during normal handling. Manufacturers and fabricators handle CVD coatings with the same procedures and equipment as standard float glass resulting in higher yields, higher profit, excellent lead times, and improved customer service.
Typical Single Flow CVD Coater
Pyrolytic CVD coatings offer several benefits:
- Lower capital investment.
- Higher yields.
- Lower manufacturing cost. CVD coatings cost ~$1/m2 vs. Sputter coatings ~$4/m2.
- CVD is an on-line process, resulting in unmatched throughput.
- CVD coatings are bonded to the glass with covalent bonds, resulting in increased shelf life, scratch resistance, and stain resistance.
- CVD coatings can be used in specialty applications like monolithic, touch screen, and anti-microbial. Conductive coating applications, like solar panels and appliance glass, are much more practical with CVD coatings.
- Special handling equipment and procedures are not needed; glass is handled and shipped with the same equipment as base glass.
- CVD coatings are not susceptible to delamination caused by moisture in the air, resulting in an unlimited shelf life.
- CVD glass is tempered similarly to standard float glass products, resulting in improved throughput and cost effectiveness.
- There is no visual differentiation between annealed or tempered CVD products. Projects requiring a mix of tempered and annealed glass benefit from a more pleasing uniform color.
While possessing several benefits from a production standpoint, CVD is not as widely used as sputtering for the following reasons:
- Until recently, CVD technology, for on-line use, was not readily available on attractive commercial terms. Stewart Engineers is now your source for "state of the art" CVD coating systems.
- CVD systems must be installed on-line at a float glass manufacturing facility, either at a new build or a retro-fit.
- Some manufacturers mistakenly believe CVD cannot be installed due to space constraints. Most float baths will accommodate an on-line CVD system.
- Some manufacturers mistakenly believe CVD can only be installed during a cold repair.
Which is best?
For a glass manufacturer, which type of coated glass is best depends on a number of factors, including where customers are located, the size and type of operation, inventory turns, desired durability, etc.
However, for most glass manufacturers, pyrolytic CVD technology is superior due to lower capital cost, lower operating cost, and higher throughput.
For downstream customers, both sputter coated and pyrolytic glass are viewed as high-performance glass products.
Architects and building owners are generally open to using both products and are primarily concerned with aesthetics which slightly favors CVD.
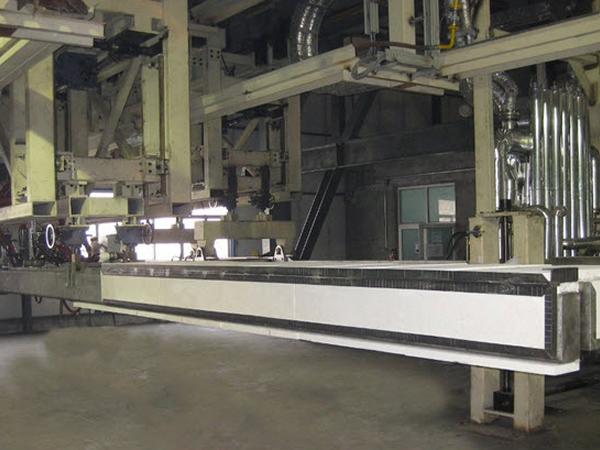

That paper is very questionable...
Costs are not realistic
Today, total vacuum deposition low-e cost is cheaper than CVD low-e
Moreover, energy and optical properties of vacuum low-e are much better than CVD low-e
CVD low-e (because of very low yield of deposition) is generating high quantities of waste (with associated pollution)
Vacuum deposition low-e remains preferred product for producers, fabricators and end customers