First presented at GPD 2019
Abstract
In the construction industries, glass is used for a wide range of products including internal partitions and display cases, but primarily it is used as architectural glass in windows and glazing systems of all building types and across all sectors. This paper aims to apply circular economy principles to the life cycle of architectural glass.
Glass is an inert material with the potential to be recycled in a closedloop system indefinitely. Coupled with the short service life of insulating glass units there appears to be a disparity between material’s potential and its current utilisation.
In the UK, we generate almost 200,000 tonnes of post-consumer glass waste each year. Much of this goes to landfill or is crushed into aggregate. Using recycled glass to make new glass products generates significant energy and CO2 savings.
This paper reviews the existing linear glazing manufacturing process and proposes a circular approach to end of life glass materials through recycling at high level, back to the glass-making furnace. Limitations, barriers and viability of such an approach are discussed and a strategy developed for the implementation of the operational system that would produce a sustainable business case for the recycling of post- consumer construction flat glass.
1.0 Pilot project and inspiration
The Burrell Collection in Glasgow U.K. was designed by Gasson, Andresen and Meunier opening to the public in 1983 to great acclaim; however, over the last decade it has unfortunately seen a steady deterioration of the building fabric and a decline in visitor numbers.
The refurbishment and renaissance project will see some 3,120m² of double-glazed insulated units in the vertical façade and pitched roof glazing systems being fully replaced along with other inventions to the façade, roofs and building services. This glass replacement scheme equates to approximately 110 tonnes of glass that will become available for re-use or recycling and must be diverted from landfill.
This refurbishment project became an inspiration and driver to research and gain a greater understanding of the current architectural glass life-cycle and to raise awareness and aim to improve the circular economy principles in the construction glass industry.
2.0 Background
According to the European Commission, construction and demolition waste is one of the largest by mass and most voluminous waste streams generated in the EU. Furthermore, a Deloitte sustainability study showed that despite its recyclability, end-of-life building glass is almost never recycled into new glass products. Instead, it is often crushed together with other building materials and put into landfills or recovered to low-grade fill applications. [1]
However, most of the flat glass used in buildings could be dismantled and recycled in glass furnaces. The flat glass industry is exploring the development of end-of-life building glass collection, sorting and recycling and is ready to use more recycled glass in its manufacturing process.
Across the EU, the proper recycling of all building glass waste compared to the business-as-usual scenario could avoid 925,000 tonnes of landfilled waste every year and could save around 1.23 million tonnes of primary raw materials annually (of which 873,000 tonnes is sand) and reduce carbon emissions by more than 230,000 tonnes annually. [1]
3 Introduction and aim
In alignment with the aims of the UN Sustainability goals, the construction & demolition industries will need to become more resource efficient and circular in its practices. While environmental ratings, regulatory drivers and project specifications will help increase the glass recycling demand, this paper presents the technical challenges of closed-loop architectural glass recycling. Furthermore, it focuses on the technical and environmental viability of end of life construction flat glass closed-loop recycling, including a study of technical challenges, barriers and viable alternatives and opportunities.
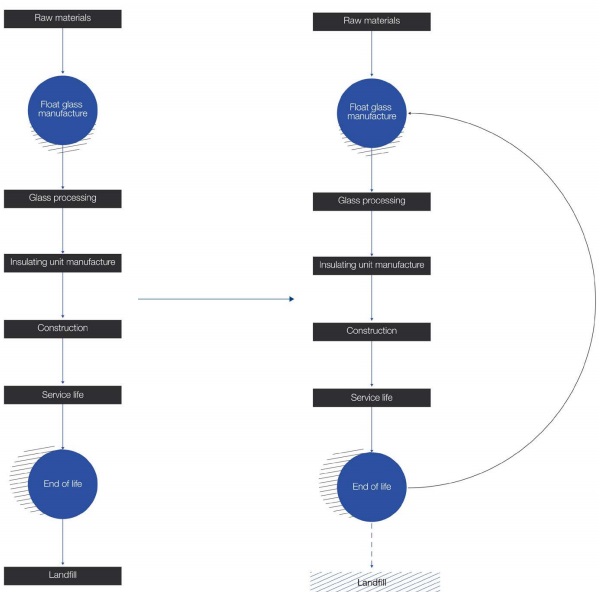
4 Circular economy and glass industry
The circular economy approach provides a framework, for designers and engineers, to build more sustainable buildings and infrastructure and decouple economic growth from finite resource consumption.
It is important to understand that recycling of materials is considered the last resort and least sustainable approach to achieving true circular economic activity because it requires the most primary energy to return the raw materials to the process cycle.
However, it is an important step nonetheless because most glass in the building envelope is currently used in the form of hermetically sealed insulating glass units whose components are not easy to separate and re-use. The widespread use of heat treatment on glass in buildings also makes that glass problematic to re-shape and re-purpose.
Around 700,000 tonnes of glass are produced in the UK each year from the three UK float lines. The manufacture of one square meter of low-e double glazing leads to the emission of 25kg of CO2 according to NSG Pilkington. [2]
Currently the life-cycle of architectural glass is in most cases linear. At the end of life 9.2 million square metres of glazing was replaced in the UK in 2013, equating to 107,000 tonnes. Together with the demolition industry, there is around 199,000 tonnes of glass available for recycling, if correctly collected.
Most of it is down cycled into aggregate or deposited to landfill. Some of the waste glass is used in manufacture of glass wool insulation, aggregates, and ballotini products, however, these are low value or non-circular material streams and they are not recyclable again and therefore are not considered a closed loop recycling processes.
These figures are likely to continue to increase in the future as more regulatory requirement are put in place to improve the thermal performance of existing building stock in a drive to reduce building energy use. [1]
4.1 Current development of the circular process
All three UK flat glass manufacturers currently use recycled glass or cullet in their manufacturing process. There is strong market demand for cullet that can meet quality and cost criteria. There are three primary sources of cullet: pre-consumer internal cullet from the glass manufacture, pre-consumer external cullet from glass processing and fabrication and finally post-consumer glass from refurbishment and demolition opportunities. Internal cullet consists of rejects or offcuts from the float line and typically makes up 20-25% of the volume of raw material mix on average in European float manufacturers. [3]
External cullet comes from the processing industry including glazing unit manufacturers. Our research found that the best-known backhauling system is operated by Saint Gobain whose glass may contain up to 35% recycled content. The quantity of external cullet used is claimed to have reduced raw materials consumption by 25%, energy consumption by 8% and CO2 emissions by 10%. [4]
Our research has indicated that up to 50% cullet content may be possible, assuming availability of the high-quality cullet required, without alteration to the existing float manufacturing processes or reduction in quality of the glass product. The demand is there, and more cullet could be collected from end of life glazing.
4.2 Grades of cullet
Not all glass removed from buildings will be suitable for moving directly back to the floatline. The quantity of post-consumer glass (that has seen service in buildings) included in the cullet flow is currently very low. The glass recycling industry has developed three primary qualities of glass cullet and these are described below.
Class C cullet is contaminated glass product not suitable for remelting. This grade may include ceramic fritted and printed glass, container glass and glass with spacer bars, putty, lead beading and the like included in the mix. This class of cullet is likely to be used for road paint manufacturer and aggregate use.
Class B is referred to as mixed cullet and may include some contamination. For example, laminated glass usually ends up in this class, as it is very difficult to completely remove the interlayer materials from the glass utilising the pulverising technique of delamination. This grade of cullet might be suitable for glass wool insulation and coloured container glass.
Class A is the clean clear cullet suitable for transportation directly to the floatline for remelt to new flat glass product. Zero contamination is allowed in this class and the float lines are very demanding of this quality. Demand significantly outstrips supply for this material class.
Contamination is the biggest technical challenge to overcome in order to increase the availability of quality cullet for the remelt process. Currently the collection method requires that contamination is very carefully controlled. Removal of the glazing units from the building site to a factory environment for disassembly appears to best provide the quality control required.
Going forward, as the value of cullet increases, development of technology may allow for lower grade cullet such as Class B to be processed and cleaned to a quality that could be used in float glass production. This has occurred in the glass container industry where there has been significant investment in machinery that can sort and improve the cullet quality, Berryman Glass Recycling facility in the UK being a good example.
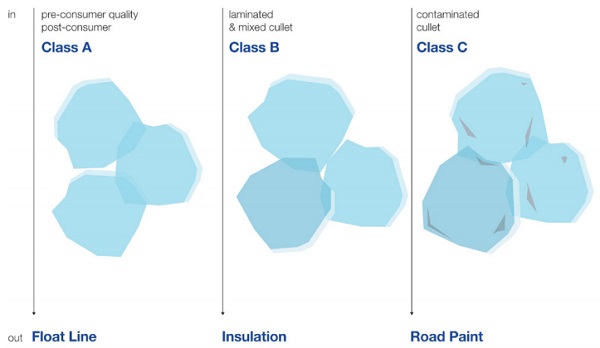
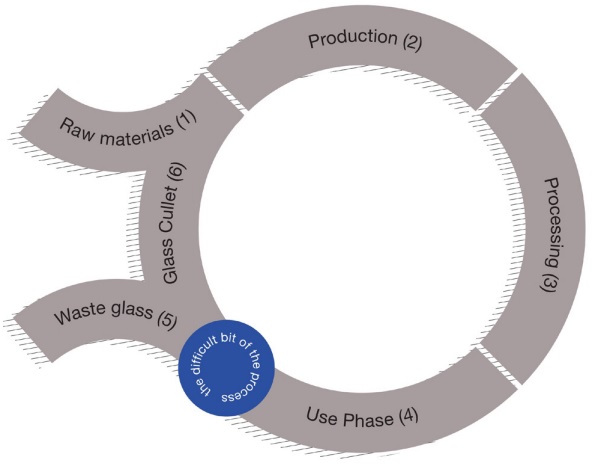
5 Benefit of closed loop recycling - Raw materials
The primary raw material of modern glass manufacture is high quality silica sand, which makes up over 70% of the mix. Due to its use in specific non-aggregate applications, and because it occurs within only a limited number of locations within the UK, silica sand is treated differently from general construction aggregate sands in terms of mineral planning.
Overall, while there is no indication from the UK glass industry of an impending critical shortage, there is, however, considerable uncertainty regarding the long-term security of silica sand supply to support the manufacturing of glass within the UK and the industry would certainly welcome additional supply options. Other European countries, like the Netherlands also list silica sand as scarce mineral resource and are looking for new sources. [5]
Glass cullet is a valid alternative for raw materials in glass manufacturing. For every one tonne of cullet used in the manufacture of float glass, 1.2 tonnes of raw material is saved. This reduces requirements for mining and quarrying, as well as the associated processing and transportation. [6]
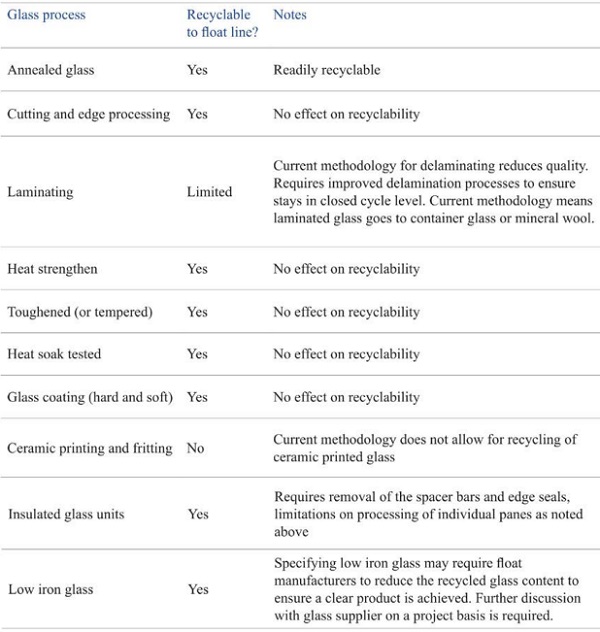
5.1 Benefit of closed loop recycling - Energy use and embodied energy
As cullet melts at a lower temperature than raw materials, for every 10% cullet added to the furnace, 3% less energy is used. British Glass have described this as 300 kWh of energy saved for every one tonne of cullet used. [6]
Previous Arup studies have calculated the embodied energy of glass at various recycled content and these calculations indicate a reduction from approx. 14MJ per kilogram of float glass with 10% cullet, 13.2MJ per kilogram with 35% cullet and reducing to 12MJ per kilogram with 70% cullet content. [7]
5.2 Benefit of closed loop recycling - CO2 emissions
A reduction of CO2 emissions of between 250-300 kg is realised for every tonne of cullet added to the furnace. [6]
5.3 Benefit of closed loop recycling - Financial
By recycling architectural glass in a closed loop cycle, materials are diverted from landfill and associated disposal costs avoided.
Additionally, once the quality cullet arrives at the float line, financial savings can be found for the manufacturer by a reduction in energy costs and subsequent reduction in emission charges (currently called “climate change tax” in the UK). Our research indicates that the current cost per tonne of cullet is less than the cost per tonne of raw material, further increasing the financial benefit of increased cullet use.
Other commercial benefits for the float manufacturer include the increased furnace life and reduced maintenance requirements, due to lower melting temperatures necessary when cullet quantity increases.
6.0 Way forward - Design for end of life
It is our responsibility as designers and engineers to consider circular economy principles and material selection from the very beginning of the design process of our projects. This will require a change in how we work and how we influence our client’s choices in material decisions.
6.1 Technical challenge - Low iron glass
There has been a steady reduction in iron content of the raw materials of standard glass production, in an effort to reduce the green coloured appearance of float glass, moving towards lower iron content and clearer glass. The use of older production run glass cullet risks increasing the iron content and there may be some correlation between iron content (and hence colour) and recycled content that needs to be appreciated as glass recycling grows. Specifying very low iron glass may reduce the opportunity to utilise recycled content.
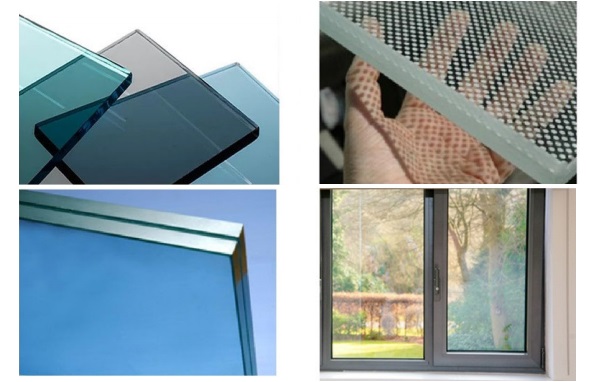
6.2 Technical challenge - Ceramic frit and tinted glass
Due to added ingredients, that have a melting point lower than clear glass, tinted or printed glass cannot be re-melted and recycled into architectural glass. While ceramic frit can be used as part of solar control strategy or aesthetics of the building, alternatives such as pigments and products like silicone based Opaci-coat are available. Furthermore, good edge seal workmanship of insulating glass units, should not be covered with ceramic frit which makes closed loop recycling more challenging or impossible at the moment.
6.3 Technical challenge - Laminated glass
Laminated glass currently provides a challenge to achieve closed-loop recycling. The composite layers need to be separated and the laminate layer removed. This is usually achieved by a pulverizing and separating machinery, crushing and grinding the glass into small pieces in the process. This size is not preferred for cullet by the float glass manufacturers but may be suitable for recycling in the container glass industry.
This means we need to review the current trend of laminated glazed units, which are often required to achieve the safety performance of the building façades. Alternatively, we can approach the challenge from the other side, and through research and technical development find a better way to delaminate glass - altering the interlayers or upgrading the delamination process.
Examples of such have been developed but are not yet in wide scale use in the UK. A company called “Delam” in Melbourne, Australia has patented a system for delaminating flat and curved laminated glass using heat, time and steaming of panes up to 1.8m x 3.5m in size. [8]
In another industry the EU’s “End of Life Vehicles” (ELV) directive will drive an increase in the requirement to recycle materials from automobiles and vehicles. In particular the recycling of laminated windscreens is of interest and adoption of technology developed for this purpose may increase the potential to recycle laminated construction glass in the future.
6.4 Technical challenges - Insulating glass units (IGU)
With perhaps the exception of uPVC window frames used in residential building, typically the framing members that support the glazing units will have a predicted service life commensurate with the building’s design life. This may be in excess of 60 years. However, the glazing units will have a predicted service life of only approximately 25 years. This is due to moisture getting past the edge seals, compromising the IGU, whilst the inert glass panes themselves could have a much longer (possibly indefinite) service life. [9]
The glazing industry is currently exploring options and developing methodologies to move away from the traditional hermetically sealed insulating glazing unit approach which is relying on sealed cavities that shortens the service life of glass façade so drastically. Current industry examples include the proprietary Closed Cavity Façade (Permasteelisa Group) and Self Conditioned Façade (Seele). However, both of these systems still tend to include conventional IGUs for thermal insulation.
Desiccant breather systems have the potential to manage the humidity of enclosed insulating air spaces without the constant input of energy and without the risk of condensation. Perhaps the most exciting prospect is for perennial facades that are designed to be refurbished in situ without opening the envelope of the building. [10]
![Figure 7: a) Equalise cavity through desiccant breather b) Perennial façade that could be repaired from either side c) Highly insulating multi-pane glazing [10]](/sites/default/files/inline-images/Fig7_5.jpg)
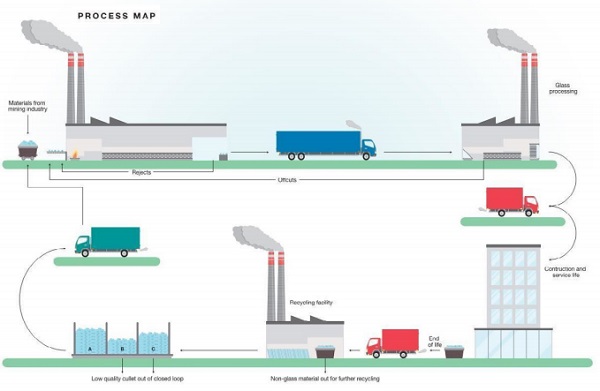
7.0 Conclusion
Glass as a 100% recyclable material, can be remelted an infinite number of times and the construction glass industry has the potential to be a perfect example of a scalable circular economy in action. Using recycled glass to make new glass products generates significant energy and CO2 savings.
In the publication Rethinking life cycle of architectural glass Arup have developed an understanding of the current recycling logistical structure and typical refurbishment construction process and supply chain. We have investigated the processes required to write a robust specification for the recycling of construction flat glass in refurbishment projects and strongly believe that sharing of knowledge and recording of pilot projects are the most important step in changing the current linear mindset of the industry.
It is our responsibility as designers and engineers to consider circular economy principles and material selection from the very beginning of the design process. This will require a change in how we work and how we influence our client’s choices in material decisions. It will require further research and innovation to overcome challenges currently posed by ceramic frit, laminated glass and insulating glass units, to ensure the best solutions for the sustainable future of the construction industry.
8.0 References
[1] HESTIN M., de VERON S., BURGOS S., 2016. Economic study on recycling of building glass in Europe. Deloitte Sustainability
[2] NSG GROUP, 2010. Pilkington and the Flat Glass Industry.
[3] GLASS FOR EUROPE, 2010. Recyclable waste flat glass in the context of the development of -end-ofwaste criteria. Glass for Europe input to the study on recyclable waste glass. June, 2010
[4] SAINT GOBAIN, 2018. Glass Cullet - The UK’s leading cullet return scheme offered by Saint-Gobain Building Glass. [online] Available at: <http://uk.saintgobain-glass.com/content/glass-cullet > [Accessed on 21 February 2018]
[5] VAN DER MEULEN M.J., WESTERHOFF W.E., GRUIJTERS S.H.L.L., MENKOVIC A., DUBELAAR C.W., MALJERS D., 2009. Silica sand resources in the Netherlands. Stichting Netherlands Journal of Geosciences 2009, Volume 88, Issue 3, pp 147-160
[6] GLASS TECHNOLOGY SERVICES, 2008. UK Glass Manufacture; A Mass Balance Study.
[7] HEESBEEN C., 2012. Glass Recycling Guide. Arup Report, Berlin February 2012
[8] DELAMINATING RECOURCES, 2013. Revolutionary New Technology For The Separation OF Laminated Glass. [online] Available at: <www.delam.com.au> [Accessed on 21 February 2018]
[9] GARVIN S., 2011. The Durability of DoubleGlazing Units. [online] Available at: < http://www.bath. ac.uk/cwct/cladding_org/wlp2001/paper13.pdf > [Accessed on 19 February 2018]
[10] DODD G., 2018, Design freedom and environmental performance beyond the constraints of the hermetically sealed insulating glass unit. Glasscon, 2018.
9.0 Contacts
Graeme DeBrincat, graeme.debrincar@arup.com, Arup
Eva Babic, eva.babic@arup.com, Arup
Rethinking life-cycle of architectural glass publication: https://www.arup.com/perspectives/publications/research/section/re-thinking-thelife-cycle-of-architectural-glass