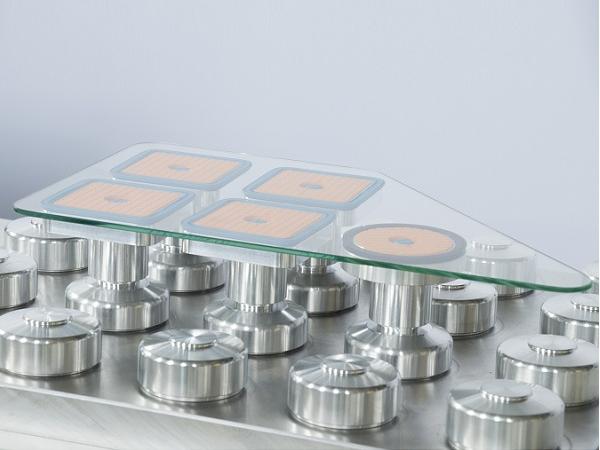
Date: 22 March 2018
Schmalz has revised its proven SQC vacuum clamping system for glass machining and made the design much more streamlined. This makes use on Bystronic glass grinding machines even simpler. Thanks to the quick-change system that can be operated without tools, setup times are significantly reduced.
Schmalz has developed the system especially for CNC machining centers made by Bystronic. This allows grinding of glass workpieces, for example designer and automotive glass on all sides. The clamping system consists of the suction cup mount (base), the suction cups and the covers for the unused vacuum connections.
The cover protects the connections and mechanical parts of the change system from contamination. When changing workpieces, users can retrofit the system very quickly: The base is fixed with a hollow bolt and can remain permanently on the machine table.
The suction cups can be easily attached, to remove suction cups only one push button must be pressed. The covers are also effortlessly attached and can be locked in a similar way to a bayonet fastener. Additional tools are not required.
The new Schmalz system is also very flexible: Depending on the glass geometry, the user can now choose between square and round suction areas. As a result, the Bystronic machines can be retrofitted on a one-to-one basis with Schmalz suction cups.
Due to the slimmer shaft of the aluminum housing below the suction area, the suction cups can be placed closer to the processing edge. The machining becomes even more precise and low vibration. Mixed operation with original suction cups and Schmalz suction cups is also possible.
The cups installed on the machine table suck in and fix panes of different geometries. Smooth machining and peripheral grinding is possible as a result. Users produce very precise and dimensionally stable parts.
An abrasion-resistant coating allows the absorption of high lateral forces between the suction cup and the glass part. The workpiece always remains securely in position even with strong lateral forces.
Glass sheets are handled particularly gently. Incorrect clamping can quickly lead to damage and expensive waste. In order to prevent this, Schmalz makes the interchangeable sealing frames of its system with the material HT1, which leaves very few marks.
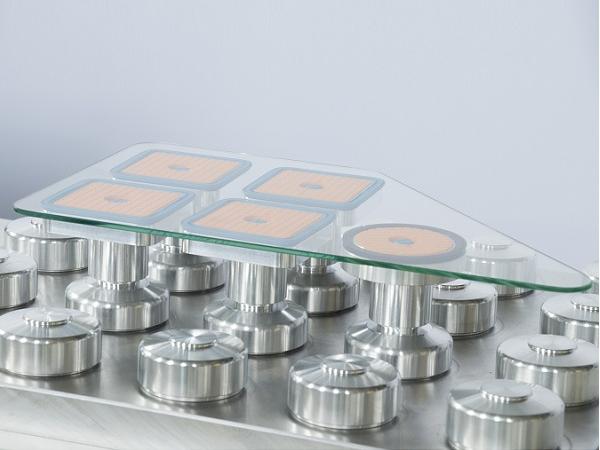

Add new comment