This paper was first presented at GPD 2023.
Link to the full GPD 2023 conference book: https://www.gpd.fi/GPD2023_proceedings_book/
Authors:
- Dr Markus Schoisswohl, Hegla New Technology GmbH & CO KG
- Dr Marco Zaccaria, AGC Glass Europe – Technovation Centre, Belgium
Scientific evidence of anthropogenic climate change, such as recent IPCC reports(1) calls for radical change in our industrial logic to drastically reduce CO2 emissions. Same applies for Flat Glass production from raw materials to building elements and various strategies shall be considered to fairly participate in saving raw materials and unnecessary CO2 output. Taking on the challenge, we concepted our process for creating value from currently disregarded used or defect glass elements. Our first step within this concept is the dismantling of IGUs, being presented in the following.
Ambition:
Investigating statistics about flat glass recycling, like the analytics of the Bundesverband Flachglas of 2019 (2), reveals, that only a small single digit percentage of flat-glass from processing or deconstruction finds its way back into float tanks. As float glass tanks have prime requirements on raw material (3), such low circular recycling rates are not surprising. In contrast they can be considered as a potential way for improvement, and we investigated the path to either supporting the float production with high quality material (recycling), or to establish raw material being in sufficient condition for reutilization, avoiding the energy intensive crushing>sorting>melting process. The recycling part is currently the most common playground, allowing according to internal assessments savings of around 0,3kg CO2eq / kg glass cullet used, as well as the corresponding avoidance of raw material of about 1,2 kg. However, in the recycling the energy and resulting emission from transport (truck: 0,03-0,160kg/tkm (4)) to central locations for crushing and melting as well as effort for crushing and sorting shall be accounted for, reducing the net effect of CO2 savings resulting from the overall process. Therefore, we considered also the second path, called “reuse”, in which due to lower scales of economy out of glass processing a distributed network may be considered.
The first step: IG2Pieces
Considering the complete stream of glass waste, IG plays a major role. Not only that the main building product is IG (e.g. Germany (5)), also in terms of waste it is not suiting circular recycling due to its composition with frame and desiccant. Out of these facts resulted our ambition to find a way to separate IG elements to pieces (IG2Pieces) to allow separation of IG elements into individual glass panes and spacer, holding the desiccant. Within the cooperation of Hegla and AGC Glass Europe, the first prototype was developed on the base of a Hegla concept to test trial industrial application of IG separation. The resulting machine holds cutting heads which slice the IG by cutting between the spacer and the glass, leaving thus the glass intact in size (unless breaks originating from edge weakened glass). This clear separation leaves mainly stains of primary and secondary sealing on the glass panes, however cut off from the spacer.
For recycling, the process provides panes separated from harmful contamination for float-tanks and in addition panes may be differentiated between coated / uncoated, allowing a best attribution of waste to requirement of remelting.
For reuse, the advantages of saving the panes are multiple. For float glass, separated panes may be subsequently cleaned from sealing residuals or cut to size for either reuse of the glass in IG or in any other application. For panes with higher added value (such as painted, tempered, laminated), the process allows reutilization of the glass from defect IGs produced, resulting not only in a reduced consumption of raw material and energy for reproduction but equally in preservation of the value added during the glass processing.
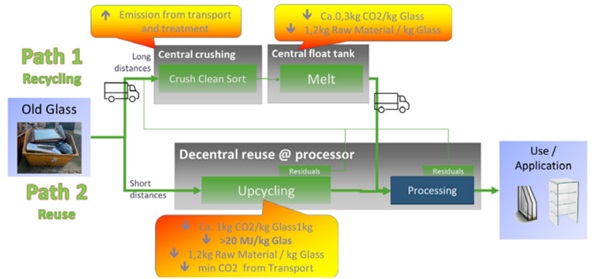
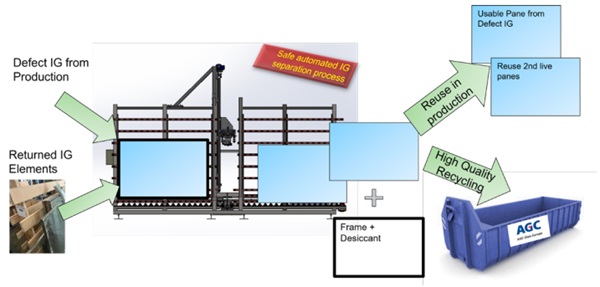
Trials of IG2Pieces and resulting products
Trials of the industrial process, prove the potential for industrial IG dismantling, with actual time for dismantling <120s for 1m2 IG. The Quality of cut unbroken glass is such that subsequent cleaning or cutting off sealing area allows reutilization of the glass.
To assess the potential for recycling and reuse, the separated panes were analysed subsequently to separation. In terms of glass types, the most found in IGUs are:
- Clear annealed
- Laminated
- Coated
- Thermally tempered
Clear annealed glass has most flexibility as it can be re-processed in full: cutting, grinding, laminating, strengthening. A recent study (6) has shown that clear annealed glass of controlled surface quality can be as performing as new glass.
Yet limited work on assessing the re-usability of laminated, coated and thermally tempered glass is available, but the elements worth assessing are:
- Adhesive properties of the PVB for the laminated glass;
- Thermal performances up-to-date as well as no corrosion for coated glass;
- Use without re-cutting for thermally tempered glass
Regarding re-cyclability, the glass type would suffice as parameters for sorting. When a glass panel has deemed of quality good enough for being re-manufactured, it can be stocked and ready for the new application. But what could be the new application? In the best-case scenario, the glass panels could be used to manufacture a new IGU (i.e. remanufacturing). In this specific case, to obtain U-values compliant with the current energy requirements, the new unit should be made of a new coated glass and a post-consumer annealed clear glass panel. Size-wise the aim should be not to trim the edges, in order not to waste material and also because keeping the glass panel as large as possible would keep the size-suitability for re-use at maximum. Furthermore, trimming the edge would mean cutting 4 edges, whilst re-sizing to fit the new size would only mean to cut along two edges. To verify the performances of this configuration it was tested if IGUs made of post-consumer glass would comply with the EN 1279, which aims at validating the water-vapour and gas permeability of the weather-seal. Three series were considered:
- Reference: IGUs made of new glass only;
- IGUs made of 1 new glass and 1 postconsumer glass, whose edges were trimmed, with application of primary and secondary sealant on previously unsealed area;
- IGUs made of 1 new glass and 1 postconsumer glass, recut to the test size, but keeping two edges where the sealant was formerly applied. The new sealant was then applied exactly on the area of former seal, properly cleaned. The results of the I index (i.e. a measure of the water intake) after the short term test (3 weeks at 58°C and 95% relative humidity) are shown in Table 1. The test is considered passed with I-index below 20. Table 1 below shows clearly that all samples easily passed the test validating that IGU made of post-consumer glass match the permeability performances of new glass. For reference, this test would warrant the CE marking.
- With the same test configurations, tensile glue tests were performed. Test is passed if all failures are cohesive (Figure 4) and if the tensile stress at maximum load is higher than 0.6 MPa at different ageing (i.e. 1 day, 4 days and 7 days). This test was easily passed by all series.
Yet full length test and the gas are to be completed, but first results indicate that positive results are to be expected. At actual state of testing the following can be concluded:
- It is not needed to trim the edges for reutilization of glass in IGUs
- The future line concept of IG2Pieces shall include a residual removal of primary and secondary sealant.
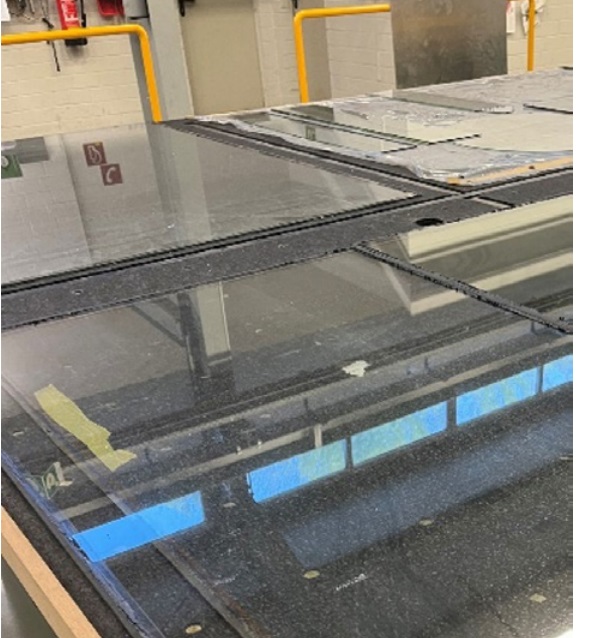
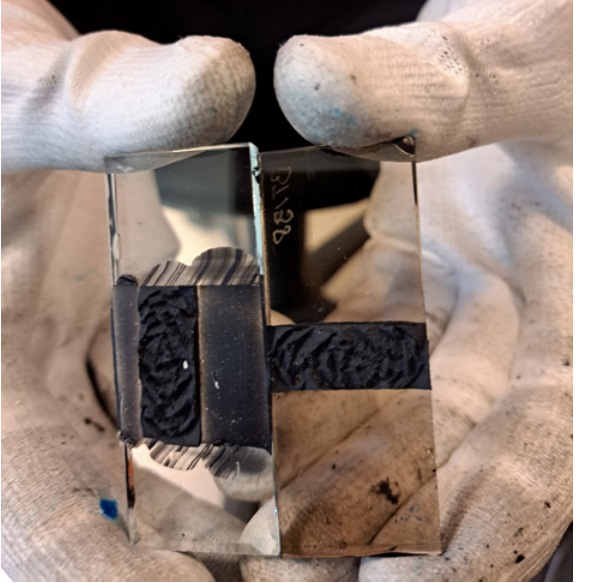

Conclusion
Based on the idea of saving greenhouse gas in glass manufacturing, the concept of IG2Pieces has revealed the potential for good fractioning of IGUs in its components, leaving the glass intact. Subsequently the glass can be either circularly recycled in form of cullet for float tanks or as 2nd hand glass being reused. Trails, creating IGUs with 1 pane of 2nd hand glass have proven so far successful, revealing the potential of real circular economy for insulated glass.
References:
[1] IPCC AR6 Synthesis Report Climate Change 2023
[2] Recycling von Flachglas im Bauwesen – Analyse des Istzustandes und Ableitung von Handlungsempfehlungen; IFT Rosenheim für BV Flachglas; Ansgar Rose, Norbert Sack Klemens Nothacker, Andrea Gassman; 2020
[3] https://eventseite.bvse.de/images/Jahrestagung2017/ Vortraege/bvse_Sack_Glas_Potsdam.pdf
[4] Ökologische Bewertung von Verkehrsarten. Michel Allekotte, Fabian Bergk, Kirsten Biemann, Carolin Deregowski, Wolfram Knörr ifeu, Heidelberg, 2020 (https://www.umweltbundesamt.de/sites/default/files/medien/ 479/publikationen/texte_156-2020_oekologische_bewertung_von_verkehrsarten_0.pdf)
[5] B+L Flachglas; Flachglasmarkt Deutschland 2022
[6] A. Rota, M. Zaccaria, F. Fiorito – Towards a quality protocol for enabling the reuse of postconsumer glass – Submitted to Glass Structures & Engineering, 2023