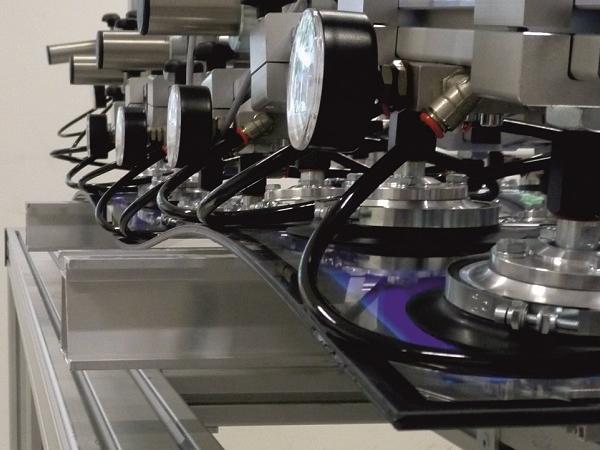
Date: 8 February 2017
Within the scope of the »TPedge« project, Bystronic glass has cooperated with scientists from the Fraunhofer Institute for Solar Energy Systems (Fraunhofer ISE) in Freiburg regarding the development of a process for the industrial production of innovative PV modules based on a Fraunhofer patent.
Numerous prototypes of these TPedge modules have now been subjected to comprehensive tests which confirm the high reliability of the module concept.
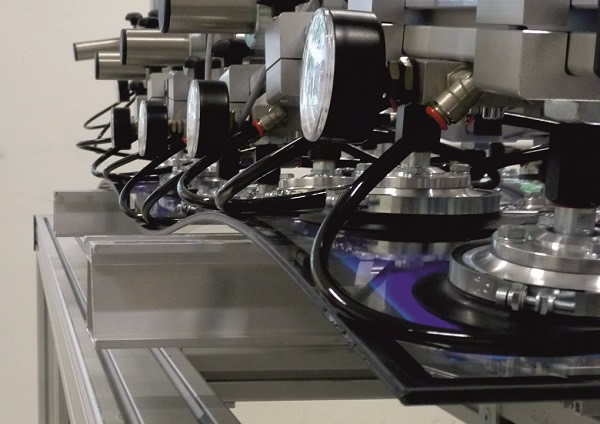
© Fraunhofer ISE
The Fraunhofer ISE mounted 70 TPedge modules on the façade of a laboratory building and subsequently put these to successful use for over three years.
The modules were produced using Bystronic glass machines and systems.
TPedge modules are edge sealed, double glass PV modules that have a great similarity to insulating glass windows. The solar cells are fixed in gas-filled spaces using adhesive pins between the glass panes.
TPedge eliminates the need for traditional encapsulation foils and the module frames so that both material costs and time consuming lamination processes are removed.
Within the scope of the project »TPedge – Development of a Technology for Edge Sealed Solar PV Modules«, the Fraunhofer ISE has cooperated with Bystronic glass in the technological development that is incorporated into the the industrial production of innovative solar module concepts.
“We have successfully taken the leap from a laboratory prototype to the standard industrial size (with 60 solar cells),” said Max Mittag, Project Manager at the Fraunhofer ISE and Tobias Neff, Solar Product Manager at Bystronic glass, explained that “With the TPedge technology, the costs for the module production can be lowered considerably – with an envisaged cycle time of 45 seconds per module line.“
The Fraunhofer ISE was able to take automated production systems for TPedge modules into operation in its »Module Technology Center« and use them to manufacture various prototypes in different setups. The industrial manufacturing processes have been developed further and optimized.
The weight of the TPedge modules have been reduced by 30 percent by utilising 2 mm thin glass. The prototypes that were manufactured together with Bystronic glass were subjected to comprehensive module tests in accordance with IEC 61730/61215.
The results confirm the high resistance and the technical maturity of the module concept. Many different TPedge design setups were tested, using the conventional glass-foil-laminate and glass-glass-laminate modules as a reference. The resistance to hail and surface load were also tested.
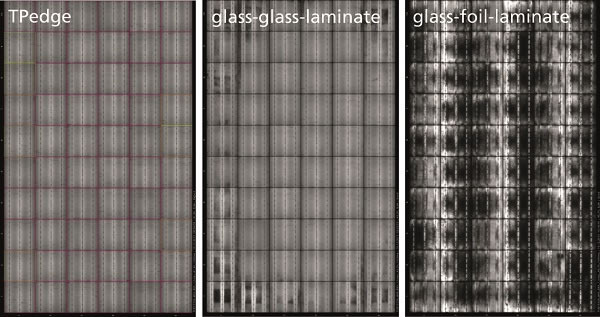
© Fraunhofer ISE
Proven ageing resistance
In the humidity-heat test, the TPedge modules with various commercial cells were subjected to a temperature of 85°C and a relative humidity of 85% over a period of 4000 hours.
The modules did not present any changes when compared with initial output measurements. In comparison, the conventional modules (glass-foil laminate and glass-glass laminate) partially displayed considerable ageing phenomenon and an output loss of up to 41 percent.
The testing of the resistance to changing thermal loads was also successfully passed. Fraunhofer ISE’s »TestLab PV Modules« verified the durability of the TPedge modules by exposing them to 400 temperature cycles (- 40°C … + 85°C) in the testing process.
Excellent mechanical resistance
Resistance to mechanical loads and hail were conducted at the Fraunhofer ISE using commercial mounting systems. The tested modules were successfully tested in various mounting positions up to a maximum pressure load of 5400 Pa.
Despite the fact that the surface load tests were repeated numerous times, a change to the output was not subsequently measured.
The hail resistance was also tested with the modules with a reduced glass thickness also being successfully tested. Critical areas of the module such as glass edges, were subjected to 25 mm large hailstones.
The tested modules passed the test without any damage and it was also possible to use the same ones for other tests.
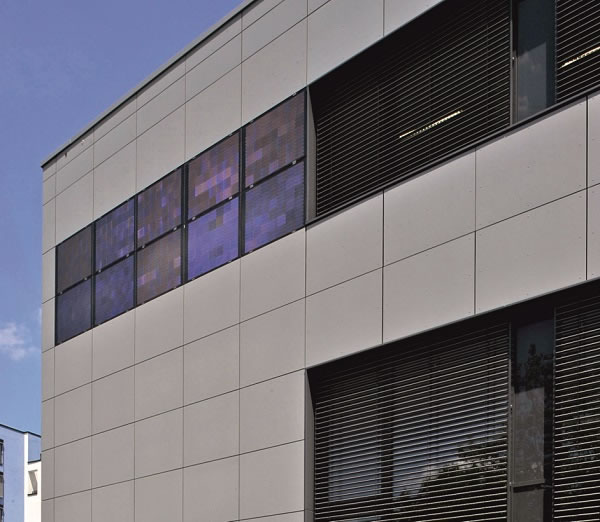
© Fraunhofer ISE
Considerable cost savings
Models for the calculation of the »Cost of Ownership« that were developed at the Fraunhofer ISE were used to calculate the specific module costs (€/Wp) for both TPedge and relevant competitive module technologies.
“The specific module costs of the TPedge module concept are around 2.2 percent below those for the conventional glass-film laminate”, said Max Mittag.
“These cost reductions are especially achieved by the lower material costs that account for around 90 percent of the total module production costs,” added Tobias Neff.
TPedge saves approx. 22% (without solar cells) or 7.5% (with solar cells) in material costs when compared with conventional modules. TPedge also saves approx. 15.4% (without solar cells) of the material costs when compared with glass-glass laminates.
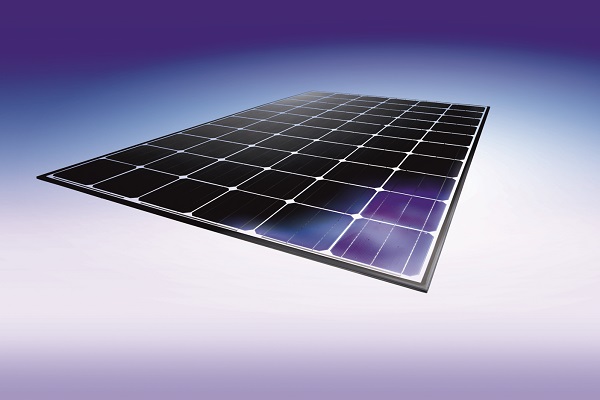
© Bystronic glass
The »TPedge« project started at the beginning of 2013 and was supported by the German Ministry for Economic Affairs and Energy (BMWi).
The Fraunhofer ISE and the project partner Bystronic glass successfully developed the TPedge module technology and industrial production possibilities further.
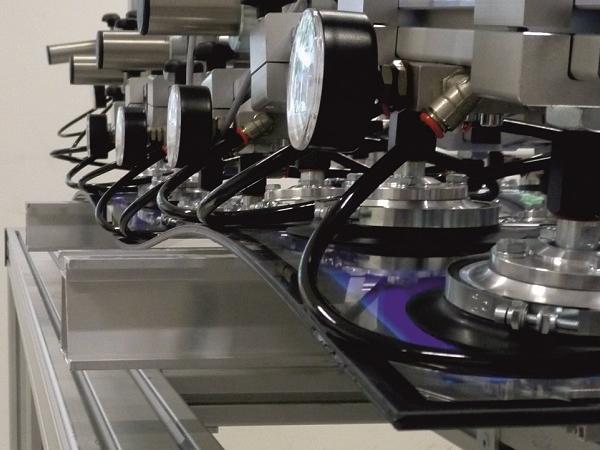

Add new comment