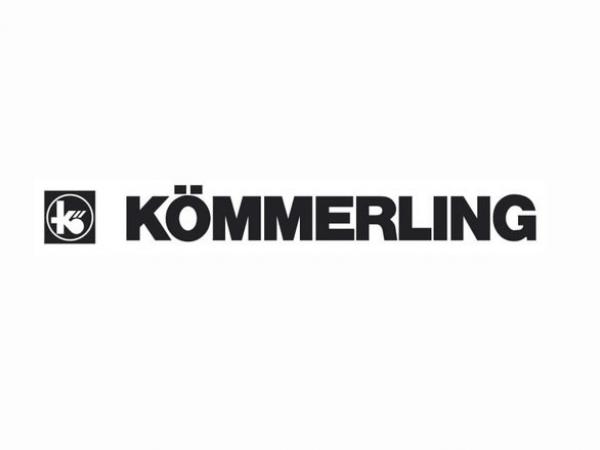
Date: 29 June 2016
Ultimately looking after the environment benefits us all. We are able to work with our customers and offer advice on how they can reduce their levels of waste in production. Many have seen considerable improvements with cost savings by implementing the recommendations which have been suggested by our Technical Service Team. There will always be some unusable material in the form of remnants which requires disposal and this is where this scheme can help." In order for companies to benefit from this service it is imperative that the sealant residue is not contaminated by general waste or rubbish.
Les Elliott, Business Manager, Glass Division, said; "The production plant in Germany puts environmental concerns high on its list of priorities and we are keen to share our philosophy and knowledge with our customers. Ultimately looking after the environment benefits us all. We are able to work with our customers and offer advice on how they can reduce their levels of waste in production. Many have seen considerable improvements with cost savings by implementing the recommendations which have been suggested by our Technical Service Team. There will always be some unusable material in the form of remnants which requires disposal and this is where this scheme can help." In order for companies to benefit from this service it is imperative that the sealant residue is not contaminated by general waste or rubbish. There are many environmental issues related to the disposal of all types and brands of waste polysulfide and polyurethane A and B part IG secondary sealants. The glazing industry's waste is generated from two main production areas:
- Following break time, or “end of shift” daily purging of dosing machines and sealant robots.
- Drums or liners of A and B part remnants which are left in the bottom of the “almost empty” 200 litre or 20 litre drums; the main area of waste concern
The uncured sealants are classified as hazardous and there is confusion regarding waste disposal as rules and regulations on this subject differ considerably from county to county within the UK. For example, in many regions it is acceptable to place fully cured “mixed” material which has taken the form of an inert rubber into normal waste skips destined for landfill. Alternatively, some regions will accept wet A part for landfill but will not allow the disposal of B part/curative. However in many counties disposing of wet A or B part material into landfill is forbidden. With the above in mind and at considerable costs to their businesses, many responsible IG producers appoint specialist waste handling companies for the collection of their waste.
As a service and at no extra cost to its customers, Kommerling collects the residue in wet form. (The sealant liners are repacked by customers into clean drums). The 200ltr drums containing liners of sealant remnants are then securely stored at the company's UK headquarters in Uxbridge. Once sufficient volume of material has been accrued it is then transported back to Pirmasens, Germany (the company's manufacturing site) and the remaining residues are extracted from each drum using an industrial mangle. In order to move such items across the borders both Kommerling and Kommerling customers adhere to recycling rules, strict international regulations and border controls and Kommerling has ISO 14001 Approval to the environmental standard.
Ken Earles, Technical Manager at Kommerling estimates that in the last 12 months the company has successfully recycled sealant residue from over 100 UK drums but there is considerable scope for more to be handled.
One customer who has been using the service for some time is Strathclyde Insulating Glass. "The remnant residue service that we receive from Kommerling has made a real difference”, said Martin Blore, Managing Director. "They have taken away the headache of our waste disposal which allows us to focus on our key activity but with the knowledge that any waste material that we do generate is being handled correctly and efficiently and without any extra cost to ourselves."
Any company interested in finding out more about how Kommerling might be able to help with their sealant remnant management should contact Les Elliott via email at les.elliott@kommerlinguk.com
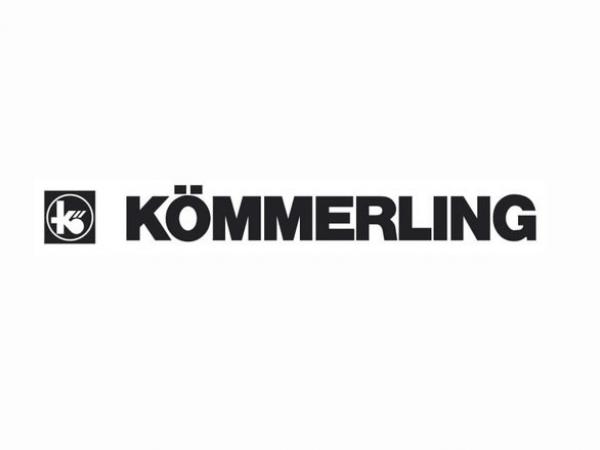

Add new comment