The ubiquitous insulated glazing unit (IGU) has been referred to as a monstrous hybrid consisting of a mixture of materials or assemblies of components from which it is not economically feasible to salvage the raw materials after their current life. In recent decades there has been an increase in the use of glass within façade systems with little consideration for end-of-life (EoL) recovery.
Technical improvements focused on improving operational energy of glazed façades can have unintentional negative consequences on the ability to recover high-value material. This research aims to assess the opportunities of avoidable waste through a comparative life-cycle impact assessment (LCIA) bound to the EoL stage and evaluate the reclamation potential of glass and aluminium from an existing curtain-walling glazing unit in different recovery scenarios.
A framework for the assessment of recovery potential of glass façade designs is proposed. Further, the technical challenges that prevent glazing systems from exploiting their re-use potential, in terms of the separation of laminated glass and adhesive connections, have been reviewed to direct future experimental research on glass façades designed for disassembly and re-use.
Introduction
A Growth in Function
Glass façade systems have evolved to serve numerous functions and meet complex technical requirements. When it comes to design for disassembly, questions arise as to whether there is a system trade-off between meeting improvements in operational energy and the ability to recover glass and other materials for re-use at their end-of-life (EoL). Early aesthetically-driven glass façade design consisted of a small material mix involving monolithic glass and mostly mechanical connections.
During the 1970s-80s, glass envelopes became more performance-driven and began to incorporate high-performance double-glazing, glass coatings and adhesivelysealed units to improve air-tightness, acoustic and thermal insulation and sun-protection. The volume of glass in buildings has since grown; triple-glazing units (TGUs) and double-glazing units (DGUs) with coatings are now considered essential elements of low and zero energy buildings.
TGUs and coated DGUs now make up 2% and 12%, respectively, of the existing glazing type distribution (EGD) in the EU. Such systems consist of more materials and more permanent connections via the use of adhesive sealants. [1], [2] Whilst single-glazing units (SGU) and early uncoated DGUs still account for 44% and 42% of the EU EGD, respectively, the field of building refurbishment to meet energy performance standards continues to grow which suggests that the large amount of glass in building stock in lower-performance systems will soon be considered unfit for functional purpose.
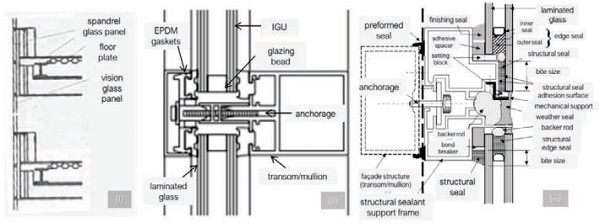
![Figure 2: i.) EE contributions over a typical building service life [3] ii.) Building split into service lives of elements [4]](/sites/default/files/inline-images/Fig2_105.jpg)
Design Implications on Embodied Energy
The distribution of initial embodied energy for building elements differs with each building. Cole and Kernan conducted research on a three-storey office building found that the façade typically contributes around 25% of the total initial embodied energy as highlighted in figure 2(i). [3] The relative contribution to the initial embodied energy (EE) is likely to continue to rise in significance due to the broad design possibilities that are explored to minimise operational energy (OE).
The significance of the EE attributed to the façade is scaled up considerably when the whole building lifespan is taken into account. This is commonly referred to as recurring EE and highlighted in figure 2(i) over, 25-, 50-, 100- year building lifespan. The building envelope is significant in terms of recurring EE, in that, in relation to the structure, it typically requires more frequent maintenance and replacement of parts. The failure rate of the IGU has been the subject of recent study. [5], [6] The multicomponent nature of the building envelope can create significant challenges in disassembly and the reclamation of glass and other materials from existing systems for re-use or recycling of component parts at EoL. [7], [8]
End-of-life can ultimately be defined as the inability for the system to fulfil its design function or meet new requirements. Changing user requirements and new developments in the area of construction, may lead to façade EoL being reached prematurely ie. every 20 years or so. [4] For these reasons, façades pose a clear opportunity to concentrate recovery methods, even more so with the advance of new materials and processing techniques that have a high-value and require more energy-intensive manufacture.
Whole-Life Energy Problem Shift
Existing policies in building construction heavily focus on improving the OE. Several researchers have studied how decisions made in the design stage of the building envelope such as DGUs with low emissivity coatings and TGUs, solar thermal collectors and building integrated solar photovoltaic panels affect the OE. [9]–[11] Consequently, other factors within the life-cycle of the façade such as EE and recovery potential are often overlooked.
Chastas, et al. reviewed previous literature on 90 residential buildings to find the ratio of EE to OE energy. It reported an EE contribution of 6–20% in conventional buildings, 11–33% in passive buildings, 26–57% in low energy buildings, and 74–100% in net zero energy buildings. [12], [13] This shifting balance has highlighted how improvements in OE, has increased the relative significance of the EE; affected by the selection of locallyavailable construction materials and methods; manufacturing energy intensity; recyclability potential; recycled content; renewability potential; potential to reduce construction waste; life span and durability; and maintenance needs.
As the energy required for operation decreases, scenarios with a higher potential for recycling and re-use can have a significant impact on the whole-life cycle. [14], [15]. However, with no internationally accepted, comprehensive and pragmatic method for assessing and comparing the recycling potential of façade materials in terms of the material choice and their embodied impact when looking at future scenarios for building refurbishment, there is little incentive for re-use. [16] [17]
Existing Process of Glass Recovery
Façades may be removed from a building as a result of full- or partial-demolition or refurbishment. The EU Landfill Directive introduced in 1999 does not present any specific glass measures. [18] Glass, as an inert material, is easy and relatively cheap to send to landfills, which does not favour the emergence of glass recycling. Based on the author’s discussions with demolition contractors in industry, it has been recognised that the most common deconstruction method involves a demolition excavator with grab/pincer attachment controlled by driver that is used to pry out metal frames.
The mixed glass falls to ground and mixed with concrete and/or brick rubble as inert waste. An onsite separation of metals, woods, concrete (including glass) is undertaken with the metals sold on to a re-use or recycling facility (~£200/ tonne) where they are usually melted down for recycling. The mixed glass inert waste is sold on for aggregate production at a much lower value (~£1/tonne) or to landfill where a landfill fee is required. The low market value, together with lack of properly organised glass collection mean that despite its re-use and recyclability potential, EoL building glass is almost never recycled into new glass products.
Independently, uncoated glass in particular is a very durable material and has high re-use potential. However, the addition of coatings, interlayers and special additives introduces difficulties in recycling. There is some uncertainty in the exact figures for flat glass collection and recycling rates for postconsumer glass. In 2007, it was found that 57% of the 5.1Mt of waste generated from the EU flat glass industry was recycled, including preand post-consumer glass. [19] Pre-consumer glass recycling rates tend to be relatively high due to them being driven by internal efficiency improvements within glass manufacturing facilities. More research into glass collection is required to quantify post-consumer recovery rates.
Circular Economy for Glass Façades
The EU Environmental Action Programme to 2020 aims to move towards a fully circular economy (CE) in which industry move towards manufacture, use and recovery models that aims to minimise the depletion of the world’s natural resources and deal with problems of waste disposal in a way that materials are reused or recycled in their best form to reduce their environmental impact by 2050. [20]
The re-use pathway mapped by the author in figure 3 is the process in which discarded components are recirculated and used for the same function without destruction.
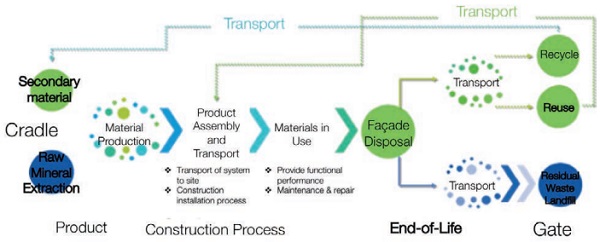
Recycling is the process in which discarded materials are reprocessed into raw materials for new products. The potential for re-using construction components in the construction sector has been acknowledged by several researchers. [21]–[23]. Most studies have focused on the recycling or re-use of narrow groups of materials such as aggregate material and steel [24], [25]. This study aims to identify the opportunities in the reclamation of flat glass from the building envelope.
Findings from an ongoing semi-structured interview conducted by the author with different stakeholders of the façade supplychain provided a useful insight into the industry’s perceptions on façade re-use. The initial findings suggest that whilst there exists some willingness for re-use, existing demand for re-use of façade product is low, largely due to a lack of specification for re-use material; lack of compatibility between re-use material and new projects due to the bespoke nature of most systems; lack of adequate supply; fear of material failure; transportation and storage difficulties; and limited separability of composite constructions. Quantified environmental benefits, improved separability of components; and improved re-use supplychain have been identified as common leverage points that could help address the existing challenges in glass façade re-use.
Study Aims
This study will present the methodology and findings from an environmental assessment conducted on an existing glass curtain-walling system to better highlight the comparative environmental savings with different EoL scenarios for glass façade system recovery. A life-cycle impact assessment (LCIA) with a substitution approach bound to the EoL stage at different service lifetimes will compare the environmental impact of different recovery routes for glass façade components.
Jin developed a multi-objective optimization tool for façade design, which is based on a whole-life value approach. [26] Existing LCIA studies that investigate the whole life-cycle consider the EoL stage based on existing technologies, without consideration for alternative recovery routes and how existing design might inhibit certain routes from being exploited. By focusing on glass façade systems, it is possible to focus on the EoL stage and make suggestions for the development of known technologies that may be increasingly utilised.
Increasingly specialised functions and components in the building envelope, have been met with more complex materials and processing methods (laminated glass and coatings); and more advanced jointing and sealing methods. There is no defined process to overcome the issues of glass façade separability with consideration of its joints and interconnectivities. This study will provide a short review of the possible deconstruction methods that could be used to identify more sustainable recovery methods salvaging glass for re-use.
Environmental Assessment Method
System Boundary
The existing study forms a process-based life-cycle impact assessment (LCIA) methodology for comparative environmental impact estimation as prescribed by the International Standard Organisation (ISO) 14040 to demonstrate to what extent the implementation of design for disassembly and re-use at the end-of-life (EoL) of glass curtain walling systems has on the environmental impact in terms of embodied energy from non-renewable resources (PENRE EE) and carbon emissions (GWP). [27] [28] LCIA relates the large number of input and output flows in terms of energy used throughout the product life-cycle, known as inventory values, to a smaller number of environmental impact themes.
The study is bound to the gate-to-grave and gate-to-cradle stage of the LCIA - highlighted in figure 4 - with a comparison of four different EoL scenarios based on existing design and potential recovery methods. The study considers the energy impacts associated with the primary energy associated with original input materials (including the energy required to extract, refine and transport fuels and the electricity used in the process), system interconnectivities, building deconstruction, material dismantling, transportation from deconstruction site to disposal/recycling/ treatment/next use site and the recycling processes from each EoL scenario based on the original material input.
The substitution approach focuses on the recovery capacities of a material. Recovery potential is the share of recovered material that could fulfil the function of primary material in the next material cycle. The scrap including treatment and recycling energy is considered as input and replaces primary resources (substitution). Energy during the construction process and use stages has not be considered as these will remain the same in every scenario for the functional unit considered. The disassembly assessment methodology framework is illustrated in figure 5.
![Figure 4: Areas of life-cycle in which this study will focus. Adapted from [29], [30]](/sites/default/files/inline-images/Fig4_96.jpg)
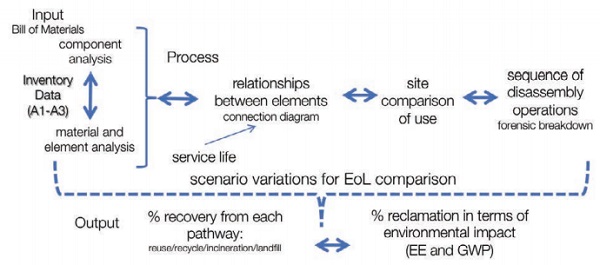
Functional Unit and System Characteristics
A functional unit (FU) provides a functional basis for fair comparison of environmental impact across the different EOL scenarios and is the reference basis all gathered data refer to. The façade system selected for this study is that used in a new educational building based in Cambridge, UK. The functional unit for this study defined as the treatment of 1 unit of triple-glazed Aluminium/Timber unitised structural glazed curtain walling, 3650 mm x 4550 mm, highlighted in figure 6(i), at EoL.
The material mass figures shown in figure 6(ii) were obtained from the author’s calculations based on construction drawings and material densities.
![Figure 6: i.) Timber curtain walling system under study [31] ii.) % mass (kg) of constituent material within FU](/sites/default/files/inline-images/Fig6_76.jpg)
End-of-Life Scenarios
Four hypothetical scenarios, explained in table 1, were constructed to draw comparisons on the EoL route that performs best in terms of achieving maximum recovery potential.
At present, the most common EoL scenario within industry is either; façade system demolition and landfill (scenario 1) or dismantle and component recycle (scenario 2). In the demolition scenario, it is assumed that materials are disposed of in landfill. Unlike the other EoL routes, no energy can be accredited in this case, as this scenario requires energy and does not deliver a surplus.
The existing environmental product declaration for the Timber-Aluminium façade system suggests a disposal scenario most similar to scenario 2. [31] Glass is considered to be downcycled in aggregate production, which requires minimal additional processing, whilst aluminium is recycled into new aluminium which requires melting down the material for reprocessing.
Scenarios 3 and 4 refer to more idealised situations, whereby re-use options are made possible due to the development of new separation technologies for component reuse (scenario 3), and performance assurance and testing for system re-use (scenario 4). The selective dismantling of façade systems for component re-use (scenario 3) offers an alternative for the existing process of downcycling glass material. In this way, flat glass sheets are recovered, to be directly re-used in the building glass industry. Table 2 shows the total % weight to each scenario of recovery.
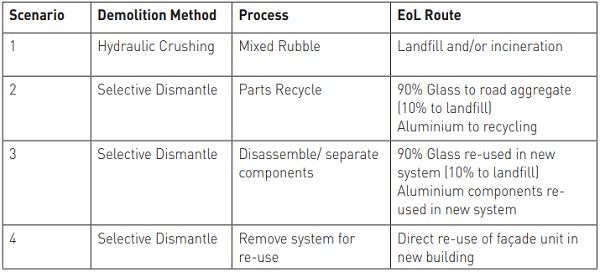
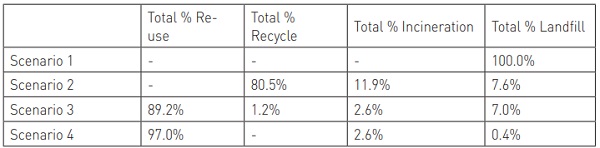
Inventory Data
Data Source
There are several databases available for input-data LCIA figures e.g. EcoInvent, ELCD. [32] For this study, inventory data was taken from the German database, Oekobaudat. Oekobaudat contains generic life cycle data sets that provide suitable averages of the environmental indicators for the building materials for life-cycle modules (A1-A3, B1-B6, C1-C4 and D). This includes the energy density coefficient, incineration coefficient, transport factor and demolition/disassembly/recycling coefficient. [33] The UK Inventory of Carbon and Energy (ICE) was used for aggregate material production data. [34] Both datasets are traceable, freely accessible and comply with ISO-14040 which allows for a comparison of all datasets to be made. [27]
Service Life
When considering re-use or recycle options, the reason for EoL is important in order to coordinate and incentivise the best recovery method.
Curtain walling framework and panel materials rarely deteriorate when considered independently. However, the multi-component nature of glass façade systems, highlighted in figure 7, means that the service life and therefore re-use potential of one component, is dependent on the service life of their nearest permanently connected neighbour component.
For system and component re-use scenarios, it is necessary to factor service life in the calculation for reclamation potential. Service life figures were established after consultation with façade manufacturers. The reclamation value for scenarios 3 and 4 at 15- and 30-years were taken as a percentage of the service life remaining. For example, laminated glass with a service life of 25 years is taken to have 40% of its initial value when recovered at 15 years.
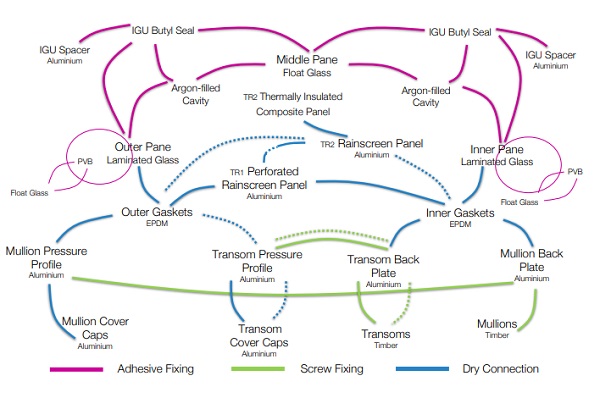
Recovery from Re-use/Recycle
ERe-use/Recycle constitutes savings that can be made in place of new production and processing from raw materials into specific component/system and can be calculated using equation 1.
Incineration refers to the process of heat recovery which can be converted into usable energy form e.g. electricity, heat or combined heat and power. EIncineration is the energy recovered through incineration of materials calculated using equation 2.
The total energy recovered from the system can be equated to the sum of the re-use/ recycle and incineration energy calculated using equation 3.
Where a particular material/component, i =1, 2, 3 etc.
Transportation
ETransport is the environmental impact caused as a result of the transport of materials, components and/or systems and can be calculated using equation 4.
The total transportation impact is a sum of all of the transportation processes from gate-tograve (scenario 1) or gate-to-cradle (scenarios 2,3 and 4) calculated using equation 5.
Transport distances in this study have been made based on the nearest recycling/remanufacturing/incineration plants.
End-of-Life
EEndlife accounts for the environmental impact due to the processes involved in demolition, waste processing, and disassembly for re-use using equations 6-8.
The environmental impact of the EoL processes can be taken as the sum of the preceding equations shown in equation 9.
Impact Assessment
The inventory data is associated with a specific environmental impact by aggregating the total quantities of all energy from the EoL and reclaim processes calculated using equation 10.
In this study, the environmental impact in terms of Embodied Energy (EE), (MJ) and Embodied CO2 (GWP), (kgCO2 eq.) for each scenario is evaluated. EE and GWP are considered important issues in the building sector. Other impacts such as acidification, eutrophication and abiotic depletion of fossil fuel have been excluded from this study as some of the inventory information is incomplete and it goes beyond the scope of this study.
Interpretation and Results
Without Service Life Consideration
The environmental impact profiles for the four different EoL routes in terms of PENRE EE and GWP are shown in figure 8, with the comparison being restricted to the EoL and next use phases. A negative environmental impact indicates that energy saving has incurred by implementing a specific EoL scenario. Without the consideration for any form of performance degradation, scenario 4 provides the most environmental savings of the 4 scenarios and can therefore be considered as exploiting the system re-use potential fully (FRP=100%).
Component re-use is able to exploit the FRP to 81.44% in terms of PENRE EE and 83.53% in terms of GWP. Scenario 3 is only made possible by a process that separates laminated glass. By re-using façade components in new systems, energy is saved from material extraction and production, which yields higher benefits than the avoidance of landfill by material recycling.
Scenario 2 shows a net avoided impact with the majority of material avoiding landfill and finding recycling potential in a second use as aggregate material or feedstock for secondary aluminium components. In this instance, exploiting FRP by 29.78% in terms of PENRE EE and 34.42% in terms of GWP, much less than that of component re-use. Further, the impacts of EoL processes themselves are shown to have the largest impact in scenario 2. Scenarios 3 and 4 are less affected by EoL processes because component or system re-use would not require the melting down of secondary materials to produce new products which is one of the most energy-intensive components of the EoL processing.
The environmental impact associated with any reconditioning or quality assurance has been taken as negligible. Although, relatively small in relation to material production, material transportation holds a more significant contribution in the component and system re-use scenarios due to the long travel distances associated with finding a suitable specialist disassembly/reconditioning plant, assuming that they are likely to be situated further afield than established landfill and/or recycling facilities. In the instance where no recycling is carried out (scenario 1), a deficit is environmental benefit is found.
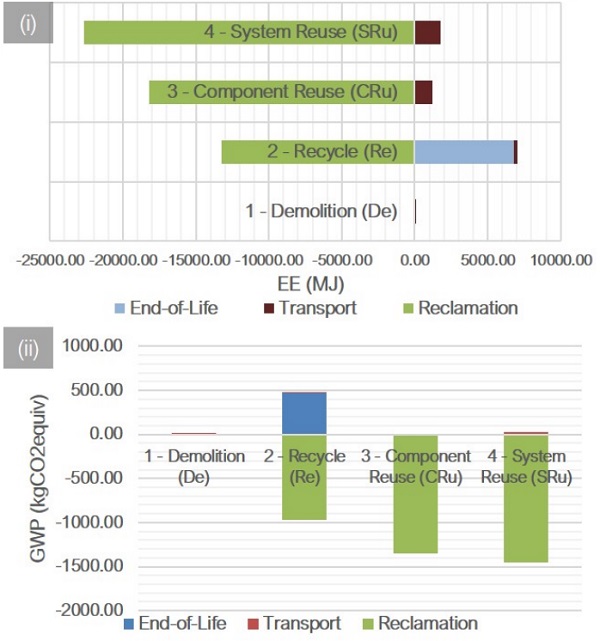
With Service Life Interdependency Consideration
It is likely that there will be some performance degradation over the façade service life. [5], [35]. In this study they have been taken as a percentage of typical service life figures, proposed by industry, illustrated by the author in figure 9.
Component re-use and system re-use at a 15- and 30-year lifetime with and without a laminated glass separation process have been considered. Figure 10 highlights to what extent the scenarios achieve the full re-use potential of the system at different service lifetimes. When service life is considered the favourability of scenarios 3 and 4 over existing scenarios are less significant.
Disassembly for component re-use (CR) opens the opportunity to extend the service life of the system. By separating laminated glass panels for flat glass re-use, they could be re-laminated for use in new systems, leading to environmental savings of the total system (42.82%). Without some form of glass separation however, the savings from CR at 15-years would be limited to only a percentage of the laminated glass SL, and at 30-years, the performance of the laminated glass can no longer be assured so the remaining re-use potential is attributed purely to a percentage SL of the framework materials and the glass recycled as aggregate material (33.13%). This is closer to the savings from scenario 2, in which the constituent materials are recycled and re-processed into new components (29.78%)
The system re-use (SR) scenario is considerably affected by service lifetime, as the system lifetime is only as long as that of the least durable part which in this case is laminated glass. At a 15-year lifetime, the re-use potential drops from 100% at 0-years to 35.22%. At 30-years, the effects of the 25-year SL of laminated glass and 30-year SL of the IGU - due to loss in integrity of the seal around the perimeter of the system - mean that the system no longer holds re-use value as a whole system. This suggests that unless there is an appropriate non-labourintensive method for providing performance assurance, component re-use with some form of glass separation yields the best potential for environmental savings when service life is considered. No established method of flat glass separation currently exists.
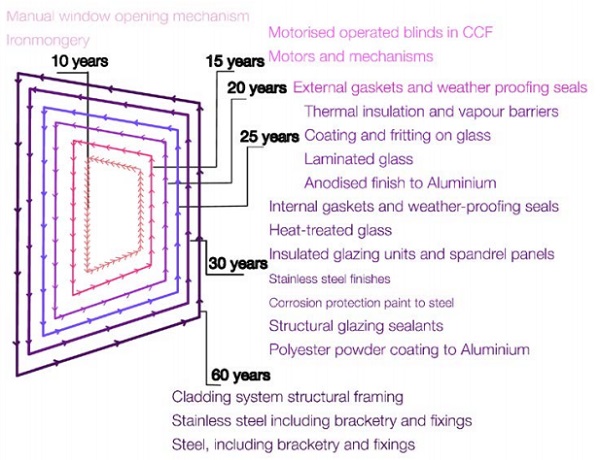
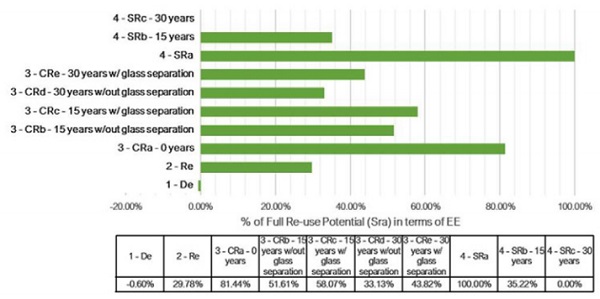
Technical Challenges in Component Re-use
Little has been done to address the challenges of composite construction and permanent jointing methods in curtain walling and the IGU that may enable component re-use.
Adhesive Connections
Due to the desired permanent nature of the joint/seal, removal of such a connection is not considered. Whilst debonding procedures depend on the adhesive used (silicone, epoxy or acrylate), adhesives that can be de-bonded or released on command hold strong potential for simplified dismantlement and recycling. Banea et al. formed a review paper that concluded that although there exist numerous proposed methods for adhesive reversibility or de-bonding, currently, there is no generally accepted solution for the disassembly of structurally bonded joints in industry. [36]
Laminated Glass
Laminated glass panels are comprised of one or more interlayers, sandwiched between two or more sheets of float, annealed, heatstrengthened or toughened glass. Laminated glass manufactured with a poly-vinyl butyral (PVB) interlayer (sandwiched between two flat glass sheets in more than 70% of laminated glass for architectural applications. [37] Lamination is completed in autoclave, whereby the interlayer bonds together with the glass panes at elevated temperature (110 – 140°C) and pressure (~0.8 MPa). [38] As a result, laminated glass can be difficult to separate when it reaches the EoL. The recovery of glass in automotive vehicles has been the subject of recent study. [39] The two existing methods of recovery have been illustrated by the author in figure 11.
At time of writing, there are no fullyestablished delaminating technologies in the EU that allow for large glass panels to be effectively separated from PVB. The existing process involves destructively crushing the laminated glass panels as opposed to separating the layers whole so that the materials have to be down-cycled into the manufacturing process rather than being reused because the separated glass fragments do not have the purity content to achieve recycling into visual glass. [39] Further, any recycling of cullet still requires re-melting at high temperatures. For these reasons, it would be pertinent to devise effective separation methods for laminated glass to enable re-use to effectively increase the service life of glass and reduce the energy costs of new glazing applications.
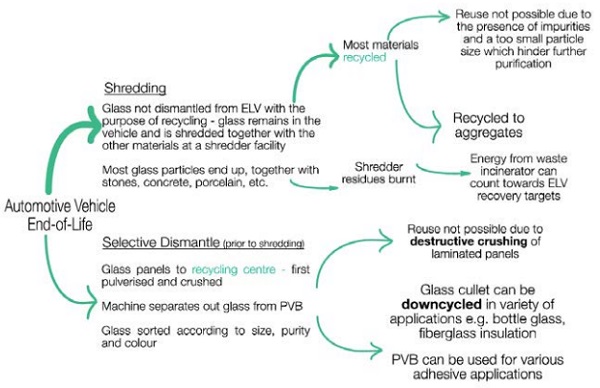
Conclusion
The principal objective of this study was to understand the environmental opportunities for architectural glass façade re-use and propose the technical methods that might exploit such recovery strategies for later experimentation. Four different EoL scenarios were developed based on current and potential future separation technologies to allow comparisons in methods for design for disassembly to be recognised.
Effective consideration of the service life of the reclaimed components is essential when assessing the feasibility of re-use. For this study, remaining service life was taken as a percentage of the estimated service life proposed by industry. In reality, it is unlikely that the reclamation value would not drop-off to zero at the end of the proposed service life from industry.
Implementing system re-use, in the instance of no performance degradation, can potentially increase environmental benefits in terms of EE by a factor of 3.4 times that of the existing recovery scenario commonly used in industry (scenario 2). In reality, there is some performance deterioration that takes place and when considering service life interdependencies, the significance in the savings made from system and component re-use are reduced.
This is as a result of the multi-component nature of glass façade systems in which their system service life is determined by the service life of their nearest connected neighbour. As a result, with consideration for service life, system re-use is less favourable over longer lifetimes due to the lack of performance assurance of the internal components. This impact is likely to be more severe in more integrated systems such as those that include motorised components with a typical service life of <15 years.
Over a longer lifetime, >25 years, and without performance testing, it could be concluded that component re-use with appropriate separation methods could makes a beneficial recovery strategy, with environmental savings in terms of EE by a factor of 1.95 times that of the recycling recovery scenario.
From an energetic and environmental perspective, component and system re-use hold large potentials in primary energy and embodied carbon savings, with some form of separation process to recover constituent components, performance assurance that could extend the theoretical service life of components together with a functional glass collection and recovery supply-chain. Without such processes in place, the recycling scenario may hold the greatest environmental benefit for the treatment of glass curtain walling units at the EoL.
Rising levels of refurbishment are likely to continue to open up opportunities to recover glass from existing stock for re-use. Further, the existing trajectory of façade design evolution creates sufficient challenges in reclaiming glass from existing systems when the façade reaches its EoL. Structural adhesives are increasingly replacing bolted connections and there may be new advances in the production of specialised glass in the decades to come. Future regulation may add to manufacturer responsibility that requests details of how new façade systems will be recovered. Technical issues of curtain walling disassembly for maximum material recovery within existing buildings must be addressed in the near future to enable re-use strategies to be made possible.
Future Research Outcomes
It is necessary to extend the study of the relative environmental impact of different end-of-life routes to different types of façade system to highlight what early-stage design decisions would achieve the most significant savings on the whole-life-cycle and recoverability of constituent materials. There exists a lack of consensus among studies calculating and documenting service life data constituent materials and systems of a glazing unit.
Different elements can respond differently to external influences allowing for each to have a different lifespan over which they degrade and/or eventually fail meaning that there are a large number of uncertainties involved in predicting the service life and therefore salvage value of components. Research into the typical depreciation rates is necessary to help define the actual residual reclamation value at any point in time during the glazed façade life.
Further, it would be useful to extend the LCIA to other indicators such as those that consider the scarcity of each resource and the avoidance of landfill. This would be made possible with access to a more complete eco-inventory database. An extended assessment should make considerations for the initial application of recycled content in designs and the use of renewable energy in material processing to ensure the benefits of re-use are not overestimated.
The existing barriers and motivations to glass façade re-use as expressed by industry through a semi-structured interview will be published in a separate review paper. While there is a lack of clarity on the properties of materials and complexity of modules in the types of construction components used in the sector, there will be significant barriers to re-use. [21] Planned research by the authors in this area looks to address the technical challenges in re-using flat glass by experimentally investigating separation methods for separation of laminated glass and joints of aluminium and glass bonded by epoxy and silicone. The development of new debonding technologies and design methods can be fed back into the environmental assessment to promote the uptake of more sustainable designs.
By considering a multi-method approach to address the challenges of re-use in the glass façade supply-chain, it will establish the opportunities to recover high-value façade material from existing building stock. Further, it will provide key indicators for future design consideration to allow for initial design and future deconstruction to clearly relate to one another to deliver buildings that truly consider whole-life energy.
References
[1] M. Hestin, S. De Veron, and S. Burgos, “Economic study on recycling of building glass in Europe,” 2016.
[2] Freedonia, “High-Performance Flat Glass - Demand and Sales Forecasts, Market Share, Market Size, Market Leaders,” 2013.
[3] R. J. Cole and P. C. Kernan, “Life-cycle energy use in office buildings,” Build. Environ., vol. 31, no. 4, pp. 307–317, 1996.
[4] S. Brand, “How Buildings Learn: what happens after they’re built,” Penguin Books. 1995.
[5] A. W. Lingnell and J. L. Spetz, “Field Correlation of the Performance of Insulating Glass Units in Buildings—A Twenty-Five Year Study,” 2007.
[6] W. Lichtenberger, “Calculating the Theoretical Life Expectancy of an Insulating Glass Unit,” in Glass Performance Days, 2005, pp. 239–242.
[7] G. Fernández-Sánchez and F. Rodríguez-López, “Importance of CO 2 Emissions in Construction Phase. Two Case Studies: New Construction and Renovated Building,” Low Carbon Econ., vol. 3, pp. 11–15, 2012.
[8] M. Herczeg, D. McKinnon, L. Milios, I. Bakas, E. Klaassens, K. Svatikova, and O. Widerberg, “Resource efficiency in the building sector,” no. May, pp. 1–128, 2014.
[9] Q. Jin, F. Favoino, and M. Overend, “Design and control optimisation of adaptive insulation systems for office buildings. Part 2: A parametric study for a temperate climate,” Energy, 2017.
[10] A. Kolokotroni, M., Robinson-Gayle, S., Tanno, S., Cripps, “Environmental impact analysis for typical office facades,” Build. Res. Inf., vol. 32, no. 1, pp. 2–16, 2017.
[11] K. K. Ramesh, T., Prakash, R., Shukla, “Life cycle energy analysis of buildings: An overview,” Energy Build., pp. 1592–1600, 2010.
[12] R. Azari and N. Abbasabadi, “Embodied energy of buildings: A review of data, methods, challenges, and research trends,” Energy and Buildings. 2018.
[13] K. Chastas, P., Theodosiou, T., Bikas, D., Kontoleon, “Embodied Energy and Nearly Zero Energy Buildings: A Review in Residential Buildings,” Procedia Environ. Sci., vol. 38, pp. 554–561, 2017.
[14] M. Balouktsi and T. Lützkendorf, “Energy Efficiency of Buildings: The Aspect of Embodied Energy,” Energy Technol., vol. 4, no. 1, pp. 31–43, 2016.
[15] G. A. Blengini, “Life cycle of buildings, demolition and recycling potential: A case study in Turin, Italy,” Build. Environ., 2009.
[16] M. D. Saghafi and Z. S. Hosseini Teshnizi, “Recycling value of building materials in building assessment systems,” Energy Build., 2011.
[17] A. Passer, C. Ouellet-Plamondon, P. Kenneally, V. John, and G. Habert, “The impact of future scenarios on building refurbishment strategies towards plus energy buildings,” Energy Build., vol. 124, pp. 153–163, 2016.
[18] EU, “Council Directive 1999/31/EC on the Landfill of Waste,” 1999.
[19] E. Rodriguez Vieitez, P. Eder, A. Villanueva, and H. Saveyn, “End-of-Waste Criteria for Glass Cullet: Technical Proposals,” 2011.
[20] EU, “Decision No 1386/2013/EU of the European Parliament and of the Council,” Off. J. Eur. Union, pp. 171–200, 2013.
[21] E. Iacovidou and P. Purnell, “Mining the physical infrastructure: Opportunities, barriers and interventions in promoting structural components reuse,” Science of the Total Environment. 2016.
[22] D. D. Tingley and B. Davison, “Design for deconstruction and material reuse,” Proc. Inst. Civ. Eng. - Energy, 2011.
[23] J. Essex, “The Market Potential and Demand for Product Re-use Product module : Construction and demolition,” no. November. 2012.
[24] J. Giesekam, J. R. Barrett, and P. Taylor, “Construction sector views on low carbon building materials,” Build. Res. Inf., vol. 44, no. 4, pp. 423–444, 2015.
[25] C. F. Dunant, M. P. Drewniok, M. Sansom, S. Corbey, J. M. Allwood, and J. M. Cullen, “Real and perceived barriers to steel reuse across the UK construction value chain,” Resour. Conserv. Recycl., 2017.
[26] Q. Jin and M. Overend, “A prototype whole-life value optimization tool for façade design,” J. Build. Perform. Simul., vol. 7, no. 3, pp. 217–232, 2014.
[27] ISO, “Environmental management — Life cycle assessment — Principles and framework,” Iso 14040, 2006.
[28] International Energy Agency, “IEA EBC Annex 57: Guidelines for Policy Makers,” 2015.
[29] A. M. Moncaster and K. E. Symons, “A method and tool for ‘cradle to grave’ embodied carbon and energy impacts of UK buildings in compliance with the new TC350 standards,” Energy Build., 2013.
[30] BSI, “BS EN 15804:2012 + A1:2013 Sustainability of construction works — Environmental product declarations — Core rules for the product category of construction products,” no. February, 2014.
[31] Schüco, “Schüco FW 50+SG.SI W x H: 3650 mm x 4550 mm Environmental Product Declaration,” 2016.
[32] L. K. Brogaard, A. Damgaard, M. B. Jensen, M. Barlaz, and T. H. Christensen, “Evaluation of life cycle inventory data for recycling systems,” Resour. Conserv. Recycl., 2014.
[33] Oekubaudat, “Life Cycle Assessment within BNB-Online- Tool eLCA and materials database ÖKOBAU. DAT,” in World SB4, 2014.
[34] P. G. Hammond and C. Jones, “Inventory of Carbon & Energy (ICE),” Mech. Eng., 2006.
[35] K. C. Datsiou and M. Overend, “The strength of aged glass,” Glas. Struct. Eng., 2017.
[36] M. D. Banea, L. F. M. da Silva, R. D. S. G. Campilho, and C. Sato, “Smart Adhesive Joints: An Overview of Recent Developments,” J. Adhes., 2014.
[37] B. Sandén, “Which interlayer for which glazing application?,” in Glass Performance Days 2015, 2015, pp. 152–156.
[38] M. Teotia and R. K. Soni, “Polymer Interlayers for Glass Lamination - A Review,” Int. J. Sci. Res., vol. 3, no. 8, pp. 1264–1270, 2014.
[39] B. Swain, J. Ryang Park, D. Yoon Shin, K. S. Park, M. Hwan Hong, and C. Gi Lee, “Recycling of waste automotive laminated glass and valorization of polyvinyl butyral through mechanochemical separation,” Environ. Res., 2015.