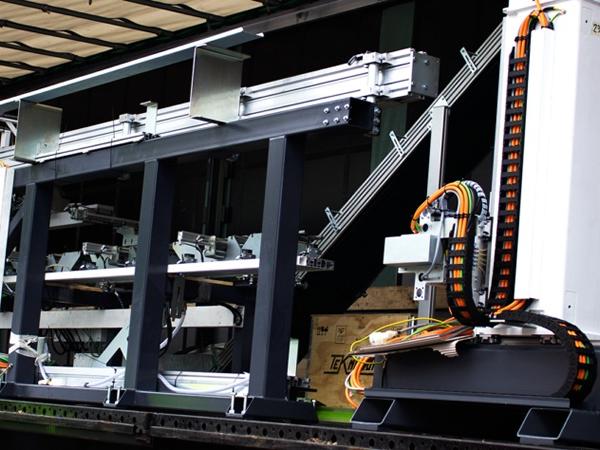
Date: 26 January 2018
It feels like Christmas all over again at TruFrame following yesterday’s delivery. The arrival of our third BDM means that we are now only awaiting our fourth and final cutting and machining centre – we can’t wait to have them all in action!
The BDM FTB-100 A2 Evo is an 8-axis, servo controlled, high-speed linear cutting and machining centre.
Here are some of the main features of our new machines:
- Twin 4-axis machining turrets provide 360° tool access, whilst operating entirely independently of each other for enhanced movement optimisation
- x3 independent profile clamps allow multiple bar processing, whilst operating on magnetic linear drives (as used on Maglev trains) that allow movement as fast as 15 m/s
- Servo-driven control modules used throughout the machine provides an overall positional accuracy of ±0.2mm (7.5 times less than BSI specified tolerances)
- Broken tool monitoring to ensure preps don’t get missed when drill bits eventually fail
- “Short-piece option” allows accurate processing of pieces as small as 195mm (which means we don’t have to cut them by hand on a chop saw anymore!)
- Type 8 acoustic cabinet significantly reduces noise emissions to provide an improved working environment for our factory operatives.
In all, we anticipate the new machining centres will provide a minimum 50% increase in overall cutting and machining capacity over what we have currently.
In addition, the enhanced accuracy will dramatically improve the finished quality of all our products and will also facilitate the transition to a different manufacturing process (crucifix welding).
Once the last of these four BDM cutting and machining centres has been commissioned we will look to introduce two single head crucifix welders.
This will see us change our manufacturing processes from v-notching to arrow heading so we can produce higher quality and more accurate welds with a restriction of just 0.2mm.
Everything that’s part of this capital investment programme, which will conclude in Easter 2018, has been geared around productivity, highly accurate product tolerances and quality.
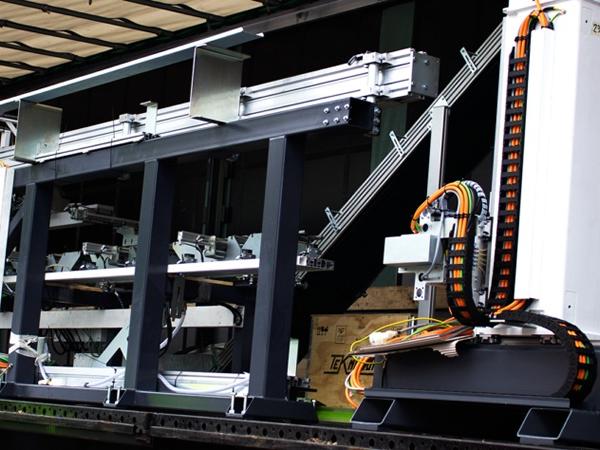

Add new comment