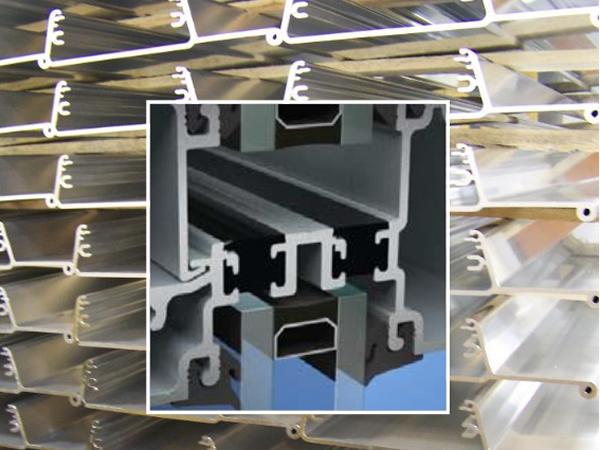
Date: 18 October 2016
The Aluminum Extruders Council (AEC) has released the most comprehensive industry-wide set of Environmental Product Declarations (EPDs) for aluminum extrusions manufactured in the United States and Canada.
The EPDs quantify the ‘cradle-to-gate’ lifecycle environmental impacts of aluminum extrusions. One EPD is for thermally-improved extrusions – of particular interest for fenestration applications – and one covers extrusions that have not been thermally improved.
Both provide data for mill finish, painted and anodized products, so architects and designers can assess the environmental impacts of finishing and thermal improvement decisions.
The EPD’s are based on a detailed study of the process inputs and outputs of 11 AEC member extruders. Thirty separate facilities, located across the U.S. and Canada, with more than 85 extrusion presses and a variety of finishing and thermal improvement facilities, were included in the study.
In aggregate, extrusion production of 1.7 billion pounds, or about one-third of the North American total for 2015, was covered in the study.
Based on a peer-reviewed lifecycle assessment (LCA), these EPDs can help designers achieve the credits required for building certification within Leadership in Energy and Environmental Design (LEED) and other green building rating programs.
Aluminum extrusion is widely used in a host of building applications, including curtain wall, window and door systems, sun shades, light shelves, louvers, interior partitions, office furniture and railings.
In addition, extrusions are widely employed in a wide variety of other manufactured products, from automobiles to lighting to solar energy mounting systems.
Lewie Smith, Chairman of the AEC’s Building & Construction Industry Promotion Team and President of Jordan Aluminum in Memphis, Tennessee, a participant in the EPD program, noted:
“We are extremely pleased to bring such a comprehensive set of EPDs to the building and construction community. Between the EPDs and the foundation LCA study, building professionals have access to new detailed information about the environmental impact of extrusions, the billet used in their production, and the downstream finishing and thermal improvement processes.”
Jeff Henderson, AEC President, added: “This project is an important step in our effort to document and improve the environmental performance of our industry in the U.S. and Canada. While LEED practitioners are a key constituency for this work, we see more and more extrusion users – particularly those in consumer oriented industries – asking for environmental information.
We are particularly pleased to see an increase in recycled content in our products as compared to the last assessment several years ago performed by the Aluminum Association.
The recyclability of extrusion without degradation of aluminum’s properties, and the robust infrastructure that exists for making recycling of extrusions a reality, is a key element of the industry’s sustainability story.”
The 11 AEC member companies that contributed data and underwent the rigorous EPD study process include Aerolite Extrusion Company, Youngstown, OH; Alexandria Industries.
Alexandria, MN; Almag Aluminum, Inc., Brampton, ON, Canada; Apel Extrusions Limited, Calgary, AB, Canada; Bonnell Aluminum , Newnan, GA; Jordan Aluminum Extrusions, Memphis, TN; Pennex Aluminum Company LLC, Wellsville, PA; Sapa Extrusion North America, Rosemont, IL; Sierra Aluminum, Riverside, CA; Tri-City Extrusion, Bristol, TN; and Western Extrusions Corp., Dallas, TX.
Copies of the two EPDs, as well as the more-detailed LCA that serves as the EPD Background Report can be downloaded at www.aec.org.
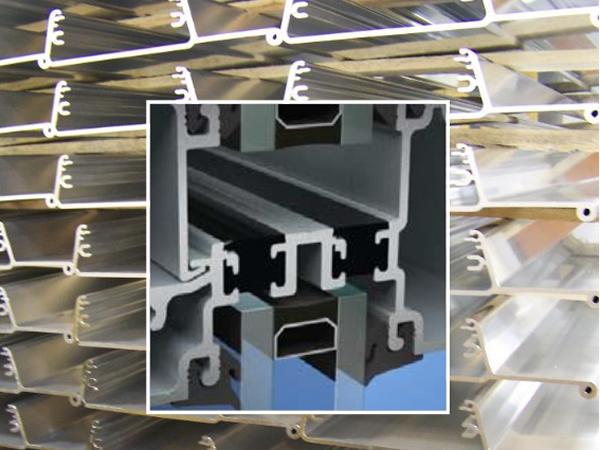

Add new comment