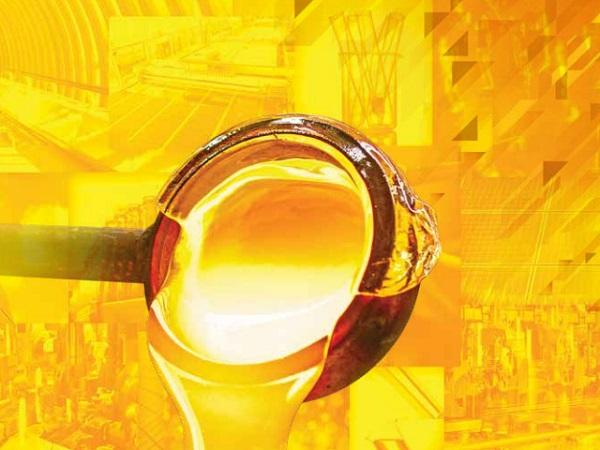
Date: 2 November 2018
Manufacturers can monitor the temperature of materials and machines using non-contact infrared (either pyrometers or thermal imagers) to ensure products will meet quality standards and market requirements.
Melting Tank
The melting tank is where the glass production process starts with sand, limestone, soda ash, and cullet feed into a furnace for melting. With the high temperatures and corrosive molten glass required for this process, it is important to measure equipment and materials exposed to extremely high temperatures that are often subject to heavy wear.
WHAT TO MEASURE
- The roof and end-wall temperatures to monitor for potential refractory failures.
- The tank bottom temperature to monitor for the erosion of the refractory lining.
- The material temperature to ensure a uniform melting process that remains within the desired temperature thresholds.
Flat Glass Production
Considerable mechanical stresses may develop in the glass as it cools down. Molten glass from the melting tank enters the tin bath through a canal and floats on top of the molten tin. The glass is then allowed to cool in the various heating/cooling zones.
Once the glass ribbon is formed, it moves to the annealing lehr where it can cool slowly. Ensuring the proper temperature of the cooling zones is essential to maintaining uniformity.
WHAT TO MEASURE
- The glass temperature in the canal, to ensure that the glass discharged by the melting furnace reaches the minimum required temperature before reaching the glass bath.
- The temperature distribution in the heating zone of the tin bath, to ensure the necessary temperature distribution.
- The temperature distribution across the flat glass ribbon, to ensure the proper temperature as it leaves the working tank.
- The surface temperature in the annealing lehr, to relieve all mechanical stress induced in the glass before further processing and packing.
- The annealing lehr discharge temperature, to ensure the required glass temperature after the cooling phase.
Container Glass Production
Container glass is a type of glass for the production of bottles, glass containers, jars, or general drinkware.In the production of container glassware, closely controlled temperatures are essential to shaping the glassware and to achieving the desired quality.
The glass gob and glass mold temperatures are very important to ensure a stable quality of the production of container glass.
WHAT TO MEASURE
- The temperature distribution of the molten glass exiting the working tank to ensure uniformity.
- The temperature gradient in the feeder to ensure continuous control of the material flow and minimize heating process costs.
- The core gob temperature to ensure the desired viscosity of the glasses.
- The mold temperature for quality control.
- The final check of materials to ensure they adhere to desired specifications.
If you want to learn more about these applications and relevant non-contact solutions (pyrometers and thermal imager), visit our website!
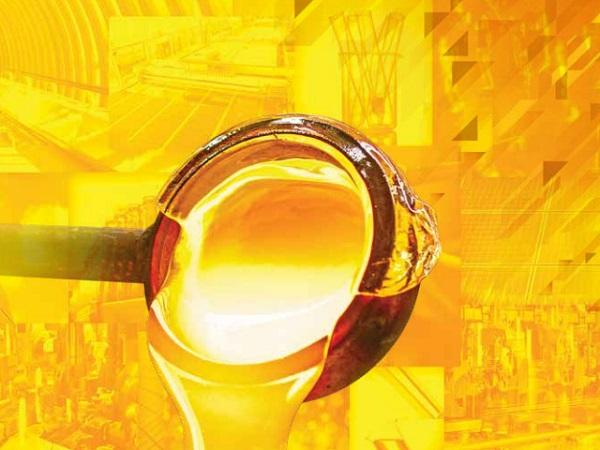

Add new comment