Source:
Challenging Glass 7
Conference on Architectural and Structural Applications of Glass
Belis, Bos & Louter (Eds.), Ghent University, September 2020.
Copyright © with the authors. All rights reserved.
ISBN 978-94-6366-296-3, https://doi.org/10.7480/cgc.7.4489
Authors:
Evelien Symoens
Ruben Van Coile
Jan Belis
Ghent University, Belgium
Glass has become an indispensable construction material. However, in extreme events such as fire, the behaviour of glass elements is still relatively unknown. The susceptibility of glass to thermal shock and its changeable material properties when subjected to high temperatures make predicting the behaviour of glass elements during fire complex.Practical applications of fire-resistant glazing, however,already exist as infill panels and frameless glass walls/doors, and are commonly used.
They are highly effective to maintain compartmentation, providing temporary protection of the unexposed side against the passage of flames and smoke and, depending on the classification, they also provide thermal insulation. This paper gives astate of the art overview of experimental research performed on glazing subjected to fire loading. Studies on temperature-dependent properties, monolithic glazing and layered glass products exposed to heating are summarised. The current shortcomings to determine the fire performance of glazing are identified and promising numerical software developments are summarised.
1. Introduction
In the past few years, several unfortunate fire incidents have highlighted the crucial need for safe building materials. Those structural materials must be able to block the spread of smoke and fire, and at the same time maintain stability during fire. Due to this motivation, assessing the performance of different building materials in a fire has become a key research field. While, extensive research has been performed on opaque building materials such as concrete, wood, steel and gypsum, research on transparent building materials such as glass is relatively scarce.
Glass’ brittle behaviour and limited tensile strength make ita highly vulnerable and fragile building material, especially in extreme loading conditions such as fire. However, the behaviour of glass elements in fire is still relatively unknown. The sensitivity of the glass material properties to elevated temperatures, together with the susceptibility of glass to thermal shock, makes the determination of the fire performance of glass elements complex. Additionally, when the glass is intended to be used as a load-bearing component, the combined effect of thermal and mechanical loading must be considered.
To comprehend the behaviour of glazing subjected to elevated temperatures, several experimental studies have been performed (e.g. Bedon 2017; Bedon et al. 2018a; Sjostrom et al. 2016). A key factor is the temperature dependency of the glass’ properties. As this information is rather scarce and scattered, a summary of the main outcomes of materials research on glass at elevated temperatures is presented in this paper. Missing data in the temperature range of 20° C to 600-700° C is identified.
On the level of glass applications (glass elements), investigations into the fire behaviour of both monolithic and layered glass products are reviewed. The main research outcomes are summarized in this paper, indicating a difficulty to extrapolate research outcomes beyond the specific test configurations as there are many influencing parameters.
This difficulty may be addressed by performing detailed parametric studies with advanced finite element modelling. However, so far little numerical research has been performed on the thermal behaviour of glass. Some promising numerical software developments are summarized at the end of this paper. However, these models still illustrate some limitations, with outcomes at times only partially corresponding to the reality.
2. Fire resistance of glass
2.1. Annealed soda lime silica glass
When considering glass applications in construction, annealed (AN) soda lime silica (SLS) glass is most commonly used. Some of its characteristics at room temperature are given in Table 1 (Haldimann et al. 2008; Le Bourhis et al. 2003). The fire and heat resistance of ANSLS glass is rather poor due to its relatively high thermal expansion coefficient and its relatively low thermal conductivity (Foraboschi 2017).
When SLS glass is subjected to a thermal loading, the low thermal conductivity induces very high temperature gradients across the surface. This means that every glass portion will contract or expand differently (Foraboschi 2017). This difference will induce stresses and since AN SLS glass has a nominal tensile resistance of only 45 MPa, this phenomenon is likely to cause breakage of the glass pane when the induced stresses exceed the tensile capacity.
Table 1: Some thermal and mechanical characteristics of SLS and BS glass (Le Bourhis et al. 2003; Haldimann et al. 2008).
2.2. Methods for enhancing the fire resistance of glass
If a better fire and heat resistance is required, borosilicate (BS) glass can be used. BS glass has a lower thermal expansion coefficient compared to SLS glass as can be seen in Table 1. Consequently, every glass portion will contract or expand less than in the case of SLS glass, resulting in a better fire and heat resistance. However, the application of BS glass in constructions is rather limited due to higher costs. Transparent ceramic glass has even a lower thermal expansion coefficient (Bach 2013). Consequently, this product can withstand very high temperatures and temperature gradients.
Another option to enhance the fire and heat resistance of annealed (AN) SLS glass is by post-processing this glass via chemical or thermal processes. In this way, heat strengthened (HS) SLS glass, thermally toughened (TT) SLS glass and chemically strengthened (CS) SLS glass can be obtained with a nominal tensile resistance of 70 MPa, 120 MPa and 150 MPa respectively (Bedon 2017). Consequently, such glass can bear larger induced stresses, resulting in a better fire and heat resistance.
Other measures to improve the poor fire resistance of glass have been taken through the creation offire-resistant glazing. An example of this kind of glazing is a laminate of different types of glass (e.g. AN, HS or TT) with transparent interlayers possessing specific functionality in case of fire (e.g. intumescent layers) (Feldmann et al. 2014). When this fire-resistant glazing is subjected to fire, the exposed glass pane will fracture but remain in place.
The intumescent layer will swell and will form an opaque insulating layer that prevents the heat from proceeding to the unexposed side. Practical applications of fire-resistant glazing exist as infill panels and frameless glass walls/doors, allowing to maintain compartmentation. They are highly effective as temporary protection of the unexposed side against penetration of flames and smoke and, also provide thermal insulation (in function of the classification). However, little to no information is available about their structural behaviour (Feldmann et al. 2014) or the combined effect of fire and structural loading.
Wired glass is another example of fire protection glass since most of the shattered glass pieces are kept together by the wire mesh, preventing the flames from going to the unexposed side. This application only provides integrity and not insulation. However, the risk of injuries remains high. As of today, glass solutions with a better safety performance are preferred.
All the previously mentioned fire-resistant solutions are examples of passive fire protection. They can be combined, with each other or with other glass elements, in insulated fire-resistant glazing units. These passive measures can be combined with active fire protection if the glass systems needs extra protection. Active fire protection (e.g. water sprinklers) can either be manually operated or automatic (Hu et al. 2016; Shao et al. 2016; Wang et al. 2018a).
2.3. Maximum allowable temperature difference in glass panes
The previous section demonstrated that the fire resistance of glass is mainly dependent on its resistance to thermal shock. Thermal shock is implied by a temperature gradient ΔT in-plane and/or through the thickness. This makes the temperature gradient an important parameter that can be used as an indicator in guidelines. Table 2 lists the allowable temperature differences for different glass types. This difference is affected by several parameters such as glass thickness and possible pre-stressing (Kozłowski et al. 2018).
Also the edge finishing, which affects the strength, has a significant influence on the allowable temperature difference. Since the edges are in many cases the location where the maximum tensile stresses appear, the glass edge strength is critical (Vandebroek, 2015). As can be seen in Table 2, the range of the allowable temperature difference goes from 22°C up to 200°C. Provided that the limits in Table 2 are not exceeded, the respective glass should be capable to withstand the induced stresses by thermal shock. Much experimental research on thermal shock has been performed in the past (Foraboschi 2017; Yang et al. 2011; Malou et al. 2013; Wang et al. 2018b). However, further investigations are still required since some past research outcomes are contradictory (Kozłowski et al. 2018).
Table 2: Allowable temperature difference for different glass types with different edge finishings (Kozłowski et al. 2018).
3. Temperature-dependent properties
When glass is subjected to fire, several properties will change when the temperature of the material increases. Various research has been performed on temperature-dependent properties (Debuyser et al. 2017; Kerper et al. 1966; Le Bourhis et al. 2003; Rouxel 2007; Rouxel et al. 2000; Shen et al. 2003; Wang et al. 2014a; Xie et al. 2011). A summary of the main outcomes is presented in this section.
3.1. Modulus of Elasticity
The Modulus of Elasticity of AN SLS glass at room temperature is equal to approximately 73 GPa as listed in Table 1 (Rouxel et al. 2000). Rouxel et al. (2000) measured the variation of this property with temperature by ultrasonic echograph. Results are shown by the crosses in Fig. 1(a). When increasing the temperature from room temperature to approximately 530°C, the measured stiffness slowly decreases linearly.
After reaching 530°C, the graph decreases more rapidly. When straight lines are drawn through both regimes, a glass transition temperature of 540°C can be found at the intersection of these straight lines. A similar slowly decreasing trend can be seen in test results presented by Shen et al. (2003) (Fig 1(b)). Compared to the research of Rouxel et al. (2000), this graph decreases a bit faster and the value at room temperature is a bit lower.
The temperature dependence of the Modulus of Elasticity for other glass than AN SLS glass, such as CS SLS glass, TT SLS glass and HS BS glass, has been investigated by Kerper et al. (1966). The results are reproduced below in Fig. 2. From Fig. 2(a) and Fig. 2(b) it can be concluded that the Modulus of Elasticity for both CS SLS glass and TT SLS glass also decreases when temperature increases. The starting value at room temperature is higher compared to values reported by Rouxel et al. (2000) and Shen et al. (2003) due to the pre-stress in the glass. It must be noted that the decrease for the chemically strengthened glass does not happen linearly. A sharp inflection is present at temperatures not much above room temperature (Kerper et al. 1966).
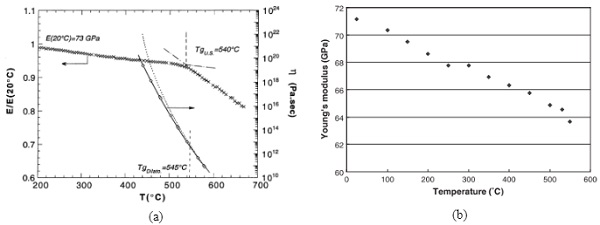
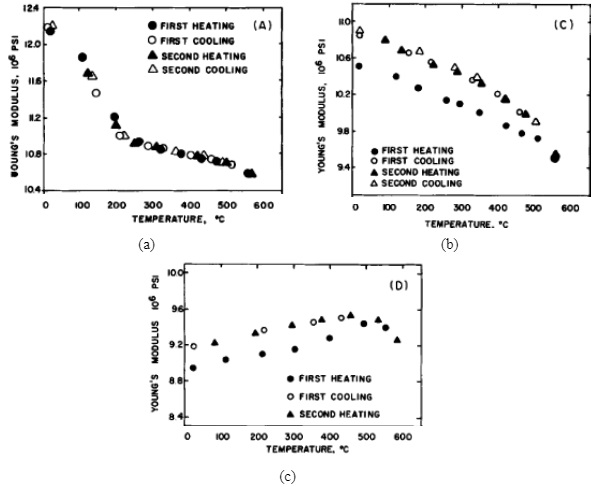
3.2. Viscosity coefficient
The previously mentioned study performed by Rouxel et al. (2000) also investigated the temperature dependence of the viscosity coefficient for AN SLS glass for temperatures higher than 420 °C. The values are measured during creep tests and are represented by the dotted line in Fig. 1(a). A rapid decrease can be observed and the curve can be described by expression (1) with R as the gas constant (Rouxel et al. 2000).
3.3. Poisson ratio
In a study of Rouxel (2007), the temperature dependence of the Poisson ratio of AN SLS glass and BS glass are compared to glass products with a different chemical composition. The results can be seen in Fig. 3(a). The starting point at room temperature for both AN SLS glass and BS glass is approximately 0.23, as previously mentioned in Table 1. For both materials, it can be concluded that the Poisson ratio monotonically increases as temperature increases. Furthermore, values for BS glass are slightly higher than the values for AN SLS glass.
3.4. Fracture toughness
The study performed by Rouxel et al. (2000) also investigated the temperature dependence of the fracture toughness of AN SLS glass. The dependency is measured using chevron-notched specimens and the results are depicted in Fig. 3(b). Different loading rates are applied i.e. 2, 4 and 8 MPa√ms-1. The toughness at room temperature is approximately equal to 0.75 MPa√m, which corresponds to values given in literature (Haldimann et al. 2008).
For each loading rate, the fracture toughness illustrates a slow weakening from room temperature to temperatures of approximately 400°C. Hereafter, all three graphs reach a minimum in fracture toughness followed by a remarkable increase at 480°C, 520°C and 540°C respectively (Rouxel et al. 2000). These temperatures represent the brittle to ductile transition (i.e. glass transition temperature) and they approximately correspond to previously mentioned values in Table 1.
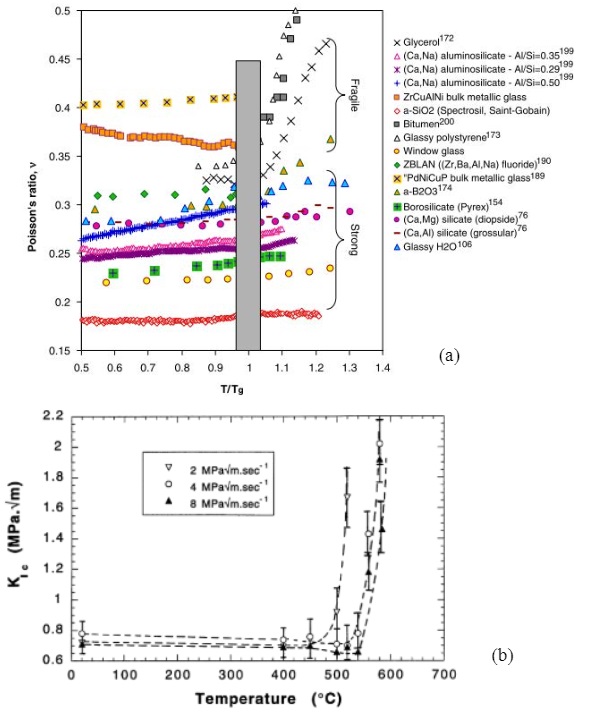
3.5. Temperature-dependent thermal properties
Also the thermal properties of both glass and interlayers have a temperature-dependent behaviour. The specific heat capacity and the thermal conductivity of glass and both polyvinylbutyral (PVB) and SentryGlas (SG) interlayers expressed as a function of temperature have been investigated by Debuyser et al. (2015). First, the authors experimentally determined the volumetric heat capacity, the thermal conductivity and the thermal diffusivity at room temperature by using the Transient Plane Source (TPS) method on eleven AN SLS glass specimens. An average value of respectively 2.042 MJ/m³K, 1.032 W/mK and 0.505 mm²/s was found.
To determine the specific heat capacity at room temperature, the volumetric heat capacity was divided with the glass density of 2500 kg/m³ resulting in a value of 816.783 J/kgK. Afterwards, the temperature dependence of the specific heat capacity was assessed by using an expression determined by Tsao (1990) and the temperature dependence of the thermal conductivity was evaluated by using an expression determined by Van der Temper (2002). The results of these calculations are depicted in Fig. 4(a) and Fig. 4(b) respectively. The same procedure is performed for both PVB interlayers and SG interlayers, for which the results are also included in Fig. 4(a) and Fig. 4(b).
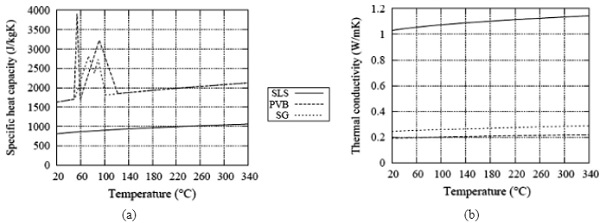
3.6. Critical breaking stress
As previously highlighted, glass subjected to thermal loading will crack when induced tensile stresses exceed the tensile resistance of the glass. The critical breaking stress is found to be temperature-dependent. This significantly influences the cracking behaviour. Both Wang et al. (2014a) and Xie et al. (2011) performed studies on the temperature-dependent tensile strength of AN SLS glass by conducting tests on a Material Testing System 810 apparatus.
Only measurements sufficiently below the glass transition temperature of AN SLS glass were performed. In this way, all stages could be considered as elastic. Both studies were performed on sufficiently preheated test samples to ensure that no thermal gradient was present. The results from Wang et al. (2014a) are depicted in Fig. 5. The tests are performed on glass panes with a nominal thickness of 6mm. The graph demonstrates a critical tensile stress that decreases from 25°C to 400°C, demonstrating a minimum at 100°C. The average breaking stress at 100 °C and 200 °C was respectively 34% and 10% smaller than the measured strength at 25°C.
The results from Xie et al. (2011) are depicted in Fig. 6. The tests in this study are performed on different glass thicknesses, each thickness tested at 25°C (Fig. 6(a)) and 200 °C (Fig. 6(b)). Comparing the results for glass panes with a nominal thickness of 6mm, the breaking stress at 200 °C was 7% smaller than the measured strength at 25°C. This result is consistent with the result from the study performed by Wang et al. (2014a). Furthermore, Fig. 6(a) and Fig. 6(b) identify a sensitivity of the critical breaking stress to the glass thickness.
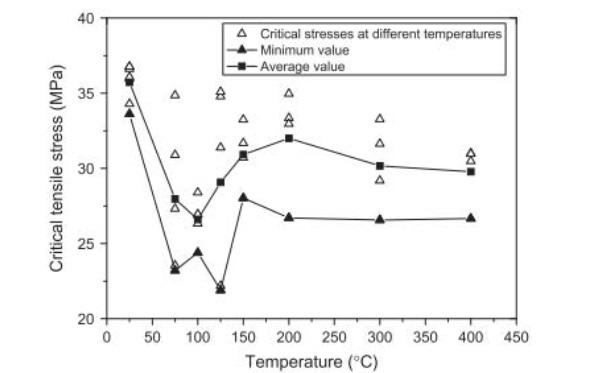
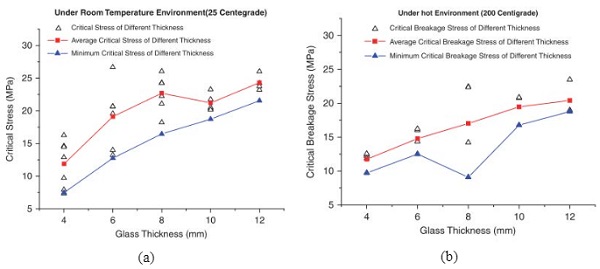
3.7. Discussion
These temperature-dependent properties are key factors in understanding the thermal behaviour of glass elements and are indispensable in numerical models. However, not all properties are determined to temperature ranges that correspond to fire loading (i.e. temperatures in excess of 400°C). Next to that, some of the mentioned outcomes are based on a limited amount of samples. Because of great randomness in the cracking of glass, more experiments should be conducted to increase the understanding of the scatter in material properties and to obtain more reliable results.
4. Literature review of tests on monolithic glass elements
4.1. Introduction: most important factors for fire design
There are several aspects which already have been investigated in literature with regard to the behaviour of monolithic glass in fire scenarios. In 2018, Wang et al. performed a sensitivity analysis of influencing factors on glass façade breakage in fire. The breakage time of the different glass elements was used as a reference. This research suggests that factors as glass panel dimensions and shading thickness may be ignored during fire safety design (Wang et al. 2018b) since they were found to have a low significance.
The sensitivity analysis indicates that fire location, the kind of monolithic glass element, and the installation configuration were the three most important factors when considering the fire safety design of glass elements in façades, as depicted in Fig. 7(a). Several studies have been performed on the most important factors highlighted by Wang et al. and will be discussed in the upcoming sections (Klassen et al. 2006; Shields et al. 2005; Shields et al. 2002; Shields et al. 2001; Skelly et al. 1991; Wang 2020; Wang et al. 2014b).
4.2. Key factor 1: Fire location
Regarding the fire location, Shields et al. performed research on a single glass assembly exposed to both a fire in the centre of an enclosure (Shields et al. 2002) and a fire in the corner of an enclosure (Shields et al. 2001). Both experiments have been performed in an enclosure with dimensions 3.6 m x 2.4 m x 2.4 m and the enclosure was instrumented to ISO room standards with single glazing units of 6 mm AN SLS glass. From both experiments, it can be concluded that the ultimate thermally induced breaking stresses ranges from 8 MPa to 17 MPa.
Compared to values quoted in the literature (see paragraph 2.1) and those obtained by four-point bending tests on glass at ambient temperatures, a scaling coefficient of 0.2 –0.3 must be used to map the experimental breaking stress of 8 MPa to 17 MPa to the theoretical breaking stress of 45 MPa. From both experiments, practical guidelines were distilled, suggesting that cracking will not occur if the local gas temperature does not exceed 100 °C, if the heat release rate does not exceed 100 kW and if the incident heat flux does not exceed 3 kW/m². However, these values can only be considered of relevance for glass panes with similar dimensions and exposure as in the test setup.
4.3. Key factor 2: Kind of monolithic glass element
To further identify the importance of the kind of monolithic glass element, Wang (2020) compared the fire performance of different glass products such as clear glass, coated glass, ground glass, wired glass and thermally toughened (TT) glass. To make this comparison, clear float glass was selected as a reference. Several studies (Wang et al. 2014c; Wang et al. 2016) identify the critical temperature difference, at which the glass panel breaks, to be slightly higher than 90°C. This temperature difference is measured between the centre of the clear float glass and the shaded edge of the glass element.
Consequently, 90°C is chosen as the critical temperature difference of clear float glass. The same parameter is measured for other kinds of monolithic glass elements (Wang et al. 2015; Wang et al. 2014a; Harada et al. 2000; Wang et al. 2014d) and these values are compared to the reference value of clear float glass (i.e. 90°C). The comparison of these different monolithic glass elements is illustrated in Fig. 7(b), where the fire performance is represented by the ratio of the critical temperature difference observed for a glass type, related to the critical temperature difference measured for clear float glass (both measured in °C). From Fig. 7(b) it can be concluded that thermally toughened glass has the best fire performance. Both Manzello et al. (2007) and Babrauskas (2011)
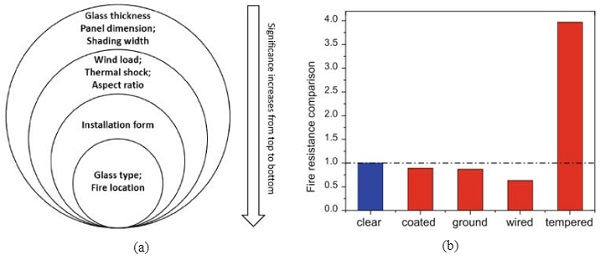
demonstrated a critical temperature difference for thermally toughened glass exceeding 300 °C. However, it must be noted that thermally toughened glass loses its integrity completely at the moment the first crack appears, while clear glass is able to maintain a certain degree of integrity between the moment of the first crack and the moment of total fall-out. Other glass elements such as coated, ground and wired glass demonstrate a smaller fire performance compared to the fire performance of the clear monolithic glass.
According to Wang (2020), the reason for this can be found in the reduced strength of the previously mentioned glass elements due to surface treatment during manufacturing. This treatment results in extra flaws present at the surface of the glass and thus reducing the strength. Here again it must be noted that the comparison is only valid for glass placed in a frame and with the same dimensions as the test setup since the comparison is based on a critical temperature difference over a certain length. No research has been performed to see how much this temperature difference changes when scaling the dimensions of the glass.
4.4. Key factor 3: Installation form
The installation form is the third important factor according to the sensitivity study performed by Wang et al. (2018b). This factor refers to different kinds of systems used to attach glass panels to the building. Glass installed in an opaque frame which causes shaded edges is the most common installation form. Several studies have been performed on frame-supported glass (Dembele et al. 2012; Wang et al. 2013; Wang 2019; Wang et al. 2014e). Wang (2019) performed a study on three different frame-supported installation forms to compare their thermal breakage.
An illustration of the different cases is depicted in Fig.8 from which (a) represents the fully exposed frame, (b) represents the horizontal-hidden frame and (c) represents the vertical-hidden frame. Since these frame conditions are commonly used in façade curtain walls, blue solar control glass panels with dimensions 600 x 600 x 6 mm³ were employed with n-heptane pool fires on a distance of 0.75m. Four different experiments were conducted for each case.
Considering case 1, every pane cracked during testing with a breakage time relatively shorter compared to case 2 and case 3. For both case 2 andcase 3, one pane did not crack, suggesting an increased fire performance for semi-exposed framing façades. Fig.9 illustrates the comparison ofthe breakage time of the different cases, suggesting that the average breakage time increases from the fully-exposed frame to the horizontal-hidden frame and finally, to the vertical-hidden frame (Wang 2019).
Next to frame-supported glass, studies have been performed on another installation form namely point-supported glass (Wang 2019; Wang et al. 2014f; Lu et al. 2018a; Lu et al. 2019; Lu et al. 2018b). Despite the fact that this installation form has a wide application, the breaking mechanism and the fire performance of these systems is not yet well understood. It is clear that the breaking process of point-supported glass will be very different compared to frame-supported glass and the entire pane will be subjected to a strong radiation from the fire. Wang (2019) performed a study on eight different point-supported installation forms to investigate the breaking mechanism and compare the
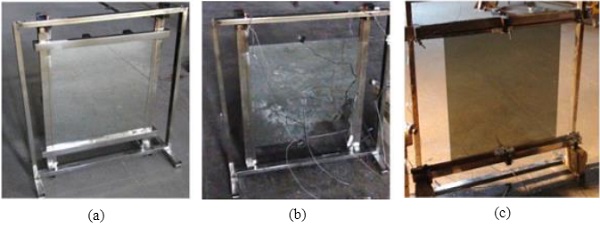
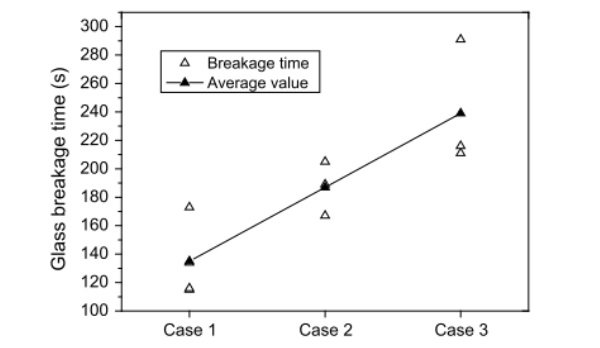
thermal behaviour. An illustration of the four-point fixed glass setup is depicted in Fig. 10 (a) and a representation of the eight different point-fixing locations is depicted in Fig. 10 (b). It must be noted that the representation of the point-fixing location is applicable for either point A, B, C and D such that the setup is kept centrosymmetric. Each form is tested three times. For each test it was observed that point-supported glass falls out easily once a crack is initiated.
This crack initiation is most of the time located at one of the point-supports, leading to the immediate fall-out of the glass. The breaking mechanism is totally different compared to frame-supported glass where cracks are initiated at the borderline of the shaded area. The same study also identified that the fixing location had a large influence on the thermal behaviour of point-supported glass. This influence can be observed in Fig.11.
The graphs from Fig. 11 (a) illustrate a shorter breakage time when the point-fixing is closer to the horizontal or vertical centre line. It also demonstrates a larger sensitivity to horizontal changes in location compared to vertical changes in location. The graph from Fig. 11 (b) illustrates that the breakage time for the diagonal locations reaches a minimum after which the breakage time increases again when all four point-fixings are close to the centre of the glass (Wang 2019).
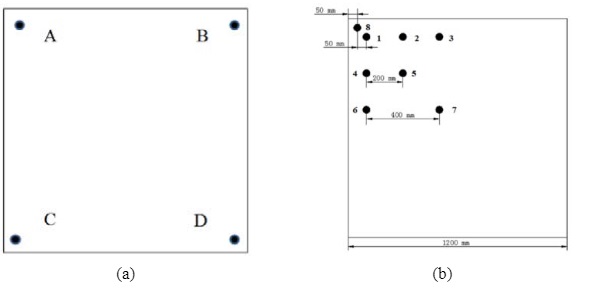
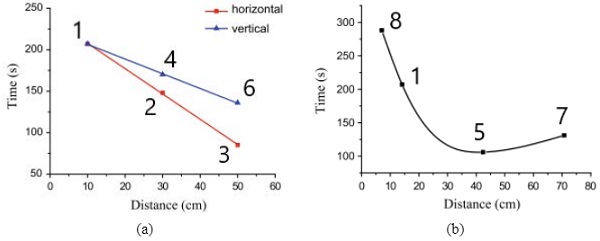
4.5. Discussion
The presented findings about the monolithic glass elements have some limitations. For each of the examined parameters, the outcomes are applicable to a certain setup with certain dimensions and a certain loading configuration corresponding to the ones from the respective study. It does not seem directly feasible to extrapolate the results. If certainty is needed about another setup and loading configuration different from the ones used in the previously describes studies, additional tests should be performed.
5. Literature review of tests onlayered glass products
5.1. Kind of layered glass product
A comparison between different layered glass products has been made by Wang (2020). Both laminated and uncoated insulated glass products were tested and compared to a clear monolithic glass pane, considering the breakage time of the glass product as indicative of the fire performance. As reference, the breakage time for a clear monolithic glass (i.e. 157 s) is considered. From the comparison in Fig. 12, Wang concluded that both laminated glass and uncoated insulated glass have a better fire performance compared to clear monolithic glass.
This is in first instance due to an extra glass pane that is (partially) shielded from the fire by the exposed panes, and also due to the increased thickness. The thermal resistance of acavity is much larger than the thermal resistance of the interlayer, resulting in a higher fire performance for the uncoated insulated glass products relative to the laminated glass. Again this comparison is only valid as a guideline when the same dimensions and thickness are assumed and when the configuration corresponds to one of the test setups.
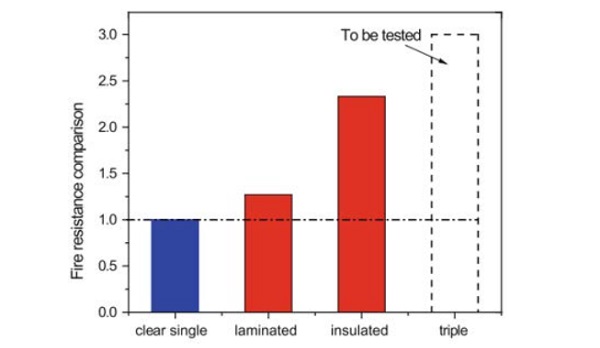
5.2. Laminated glass panes
Since structural glass is always laminated with a certain interlayer material, the behaviour of the interlayer is an important factor. The glass transition temperature of common interlayer materials is situated around 18-55°C which makes the interlayer a critical component. Little research has been performed on the behaviour of laminated (safety) glass in fire conditions. The study by Debuyser et al. (2017) considered both monolithic and laminated glass products heated by radiation panels. The monolithic specimens had nominal thicknesses of 6, 10 and 15 mm with two extra specimens of 6 mm with a pyrolithic low-E coating.
The laminated specimens consisted of three glass panes with a 6-10-6 mm composition, all consisting of clear glass and each bonded with either a PVB or SG. Testing the laminated specimens, different phenomena were observed. At first the exposed glass pane cracked. Later on, gas bubbles occurred in the interlayer closest to the exposureas can be seen in Fig. 13 (a). Gradually these gas bubble became bigger and more widespread. After a certain amount of time the most exposed interlayer started liquefying (Fig. 13(b)). The interlayer on the exposed side of the laminate discoloured as illustratedin Fig. 13(c).
After that, all phenomena repeat themselves for the second interlayer present in the laminate. The measurements of these tests led to the conclusions that a gas formation reaction occurs at an interlayer temperature of 90 °C for PVB material and 150 °C for SG material, regardless of the applied heat flux. All phenomena appeared for both the PVB and SG specimens but the gas bubbles were generally smaller in case of SG. Due to these reactions, the radiation transmitted through the glass system could be expected to be time-dependent.
However, the absorptance and the transmittance proved to be constant. The constant transmittance was due to the reflection that mainly occurred at the exposed surface. Therefore, the interlayer reactions do not have an effect on the radiation transmitted through the glass system. Testing the monolithic specimens led to the conclusions that absorptance increases with increasing thickness and transmittance decreases with increasing thickness. This is aresult of through-the-thickness absorption. The reflectance remained more or less the same for the clear monolithic specimens regardless of the thickness.
However, if a low E-coating is present at the exposed surface, the reflectance is significantly higher hereby resulting in a reduction of the absorptance and transmittance. The reduced transmittance is advantageous for the barrier concept and the reduced absorptance is advantageous for the glass itself, resulting in smaller thermal gradients. Therefore, thermal fracture is delayed or even completely avoided (Debuyser et al. 2017).
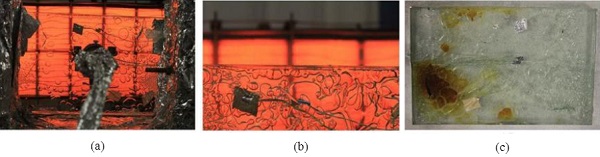
5.3. Laminated glass load-bearing elements
Structural glass beams consist of laminated glass panes and are, in some cases, combined with other materials to provide post-breakage strength and ductility. However, so far limited experimental research has been performed on structural glass beams subjected to elevated temperatures and fire loading. Veer et al. (2001) tested several glass beam configurations in a four-point bending setup with a propane burner at a constant distance which ensured a temperature of 650°C at the exposed surface of the beam. All beams had a length of 400 mm and a height of 40 mm.
The glass beam with a continuous cross-section (three glass layers of 3 mm bonded with a polycarbonate foil) performed well in this setup as long as the exposed region to high temperatures remained small. However, complete replacement of the beam after the fire was required due to severe damage of the interlayer. The glass beam with a discontinuous cross-section (three glass layers of 3 mm, with glass segments organised in an overlapping pattern, bonded with a polycarbonate foil), did not perform well in this setup. Local debonding of the segments near the heat source caused buckling of the laminate as depicted in Fig. 14(a).
However, this problem may be (partially) solved by an additional outer layer to form an insulating cavity (Veeret al. 2001). The same setup was applied by Bokel et al. (2003) to investigate the difference between a commercially available product (i.e. Pyroguard®) and a custom made alternative of three SLS glass layers of 3 mm bonded with epoxy resin. Both specimens exhibited charring of the interlayer after few seconds only, indicating a limited fire performance. The epoxy interlayer of the custom made alternative started charring at a higher temperature than the epoxy interlayer of Pyroguard®, indicating that the chemical nature of the interlayer influences the fire performance (Bokel et al. 2003).
Full-scale experiments to investigate the structural response of laminated glass beams to fire loading were performed by Louter et al. (2016). Three beams were tested (AN, HS and TTresp.) with a cross-section consisting of three glass layers of 10 mm bonded with SG foils. All beams had a length of 1000 mm and a height of 100 mm and were subjected to four-point bending with a fixed load of 115 kg. The lower 7 cm of the beam was directly exposed to the fire loading (i.e. standardized heating curve for fire testing) while the remaining 3 cm at the top of the beam was used to close the oven with fire protective panels. An illustration of the laminated glass beam after testing in this setup is depicted in Fig. 14(b).
The results illustrated a significant offset between the furnace temperature and the temperature inside the laminate. The temperature in the AN glass beam proved to increase fastest, followed by the temperature in the HS glass beam and after that, followed by the temperature in the TT glass beam. Detailed research is needed to investigate if this difference in heating rate is related to the difference in pre-stress. All beams collapsed upon reaching a temperature of 780 °C. Consequently, the difference in heating rate caused the AN glass beam to fail first, followed by the HS glass beam and after that, followed by the TT glass beam (Louter et al. 2016).
As already mentioned, laminated glass beams can be combined with other materials, such as timber, to provide post-breakage strength and ductility. Timber-Glass composite beams already proved their potential at ambient temperatures but the performance in case of fire is however a concern. Full-scale experiments on these Timber-Glass composite beams were performed by Sjöström et al. (2020). Each beam has a length of 3920 mm and a web height of 190 mm consisting of three glass layers of 10 mm bonded with PVB interlayer.
The web was bonded to a groove in the timber flanges by using epoxy adhesive. The beams were subjected to four-point bending and the bottom part of the beam was exposed to a fire loading. The setup of the beams before testing is depicted in Fig. 14(c). All glass webs failed early in the test. Due to the shading flange, the lower (and upper) edges of the inner glass panel remain colder, resulting in large thermal gradients. Consequently, the fire performance of the Timber-Glass composite beam is less than the fire performance of the glass web itself. However, better results can be obtained when the inner pane consistsof a glass with better fire performance (e.g. TT instead of AN) or when the inner pane has a reduced height compared to the outer panes (Sjöström et al. 2020).
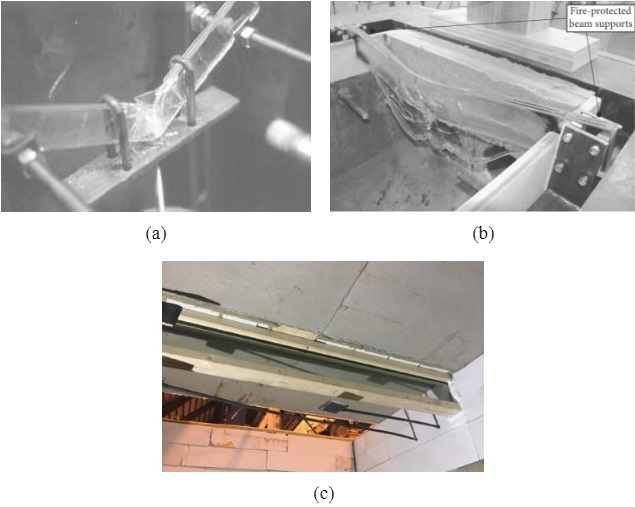
5.4. Double glazing
From the comparison by Wang (2019) in Fig. 12, it was already concluded that double glazing has a better fire performance compared to clear monolithic single glass. Several studies have been performed to investigate the behaviour of double glazing subjected to a fire (Choi et al. 2018; Klassen et al. 2006; Shields et al. 2005; Wang 2019; Wang et al. 2017a; Wang et al. 2017b; Wang et al. 2017c). Wang et al. (2017b) investigated the effect of the air space thickness between a fire side pane and an ambient side pane.
The double glazing samples from this research consisted of two clear float panes with each the dimensions 600 x 600 x 6 mm³. An illustration of the cross-section with locations of the thermocouples is depicted in Fig. 15(a). An air space of respectively 6mm, 9mm and 12mm was tested with three different samples for each case. The breakage time of the ambient side pane is the most important parameter to investigate the effect of the air space thickness. The experiments demonstrated an increase in the breakage time from 495 s to 511 s with increasing air space thickness.
Wang et al. suggest this increased thermal resistance is predictable since more air has to be heated when the air space thickness increases. This trend is also demonstrated in Fig. 15(b) where the temperature variation of the ambient side pane for every air space thickness case is presented. Wang et al. found that the air space thickness had no significant influence on the fall-out fraction. However, double glazing with a larger air space thickness had more difficulty to keep its integrity when subjected to fire since the failing of the spacer will increase the possibility of fall-out occurrence (Wang et al. 2017b).
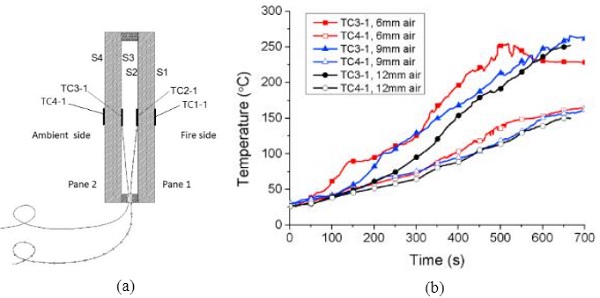
5.5. Discussion
The presented findings about the layered glass products have the same limitations as discussed for the outcomes of the monolithic glass elements. The outcomes of each examined parameter correspond to a certain setup and loading configuration, leading to the fact that, in principle, additional tests should be performed when considering another setup and loading configuration.
6. Numerical modelling
If additional tests have to be performed each time the setup changes compared to the setup from the performed studies, a lot of time and money would be spent. A solution to this problem could be the application of advanced finite element modelling for parametric studies. However, the numerical modelling of the behaviour of glass to fire loading is still in an early stage.
6.1. Crack prediction
A finite element program, called EASY, was developed by Wang et al. (2012) to investigate the dynamic three-dimensional thermal stress distribution in window glass under thermal loading. This stress model is used as a basis to predict cracking, considering the breakage of glass to be fully dependent on the stress distribution inthe glass. The authors simulated the stress distribution by using FORTRAN 90. The temperature rise ΔT(x,y,z) relative to the initial state is derived from which the associated straincan be calculated with the use of the coefficient of thermal expansion.
The corresponding three-dimensional thermal stress distribution is derived from the stress-strain relationship and by using the effective Newmark method an integration in time is performed to end up with the dynamic three-dimensional thermal stress distribution. To predict the failure of the glass element, the Coulomb-Mohr criterion is employed since this criterion predicts well the failure of brittle materials. It states that a crack will initiate when the following condition (2) is met (Wang et al. 2012):
with σ1and σ3 as the maximum and minimum principle stresses respectively and Sυt and Sυc as the ultimate tensile and compressive strengths respectively. For more information about the implemented expressions, formulas and methods, reference is made to Wang et al. (2012).
6.2. Crack propagation
The authors of the previously mentioned finite element model EASY, Wang. et al., extended their numerical model with crack propagation and glass fall-out. The enhanced version is called GLAZ-CRACK (Wang et al. 2014g). When a glass panel fractures, three different failure modes need to be considered namely mode I (crack opening), mode II (crack-shearing) and mode III (crack-tearing). The stress intensity factors and the energy release rates at the crack tip of these failure modes are used to evaluate the characteristics of the fracture.
The stress intensity factors (KI, KIIand KIII) are all proportional to the stress distribution over the glass panel. Since this distribution is calculated with the previously mentioned software program EASY, the stress intensity factors can be determined. Subsequently, the energy release rates can be calculated since they are in function of the stress intensity factors (Wang et al. 2014g).
As previously mentioned, a crack initiates when the crack initiation criterion is met. From this moment, the crack will grow when the crack growth criterion is met. Three different criteria are described in this study namely a stress intensity factor-based criterion, an energy release rate-based criterion and a stress intensity factor-based maximum circumferential stress criterion. All three criteria are a combination of the different fracture modes. If a crack growth criterion is met, the direction and the speed of the crack propagation is calculated.
To follow the crack tip movement, elements around the tip are refined at eachtime step. In this way, additional nodes and elements are created to model the crack propagation more accurately. The mesh topology of the respective location is restored to its pre-refinement level once the crack tip has moved on (Wang et al. 2014g). For more information about the implemented formulas, the author refers to the detailed paper of Wang et al. (2014g).
Although the numerical outcome illustrates a good agreement with the reality, the model is not able to predict multiple crack paths. In reality, a glass element subjected to thermal loading has several crack propagation tracks. The GLAZ-CRACK model is only able to model one crack path. However, Wang et al. demonstrate this crack path to bein good agreement with one of the crack propagation tracks from the reality.
7. Summary and conclusions
Increasing glass applications arise due to its aesthetic transparent performance, but a clear understanding of its fire performance still requires research. This paper presented the state of the art in research on the behaviour of different glass elements subjected to elevated temperatures. The fire resistance of annealed SLS glass is found to be relatively poor due to its large susceptibility to thermal shock. The fire resistance can be enhanced by post-processing the glass element thermally or chemically. Another possibility is using BS glass since its thermal expansion coefficient is lower. Fire-resistant glass concepts have been invented to prevent flames and smoke from going to the unexposed side. However, these applications only stay intact for a certain amount of time, and are not designed for a load-bearing function.
Several temperature-dependent properties have been summarized in this paper. These are needed for a clear understanding of the thermal behaviour of glass elements subjected to elevated temperatures. The modulus of elasticity, the viscosity coefficient and the critical breaking stress demonstrate a significant decrease with increasing temperature. The Poisson ratio and the thermal properties (specific heat capacity and thermal conductivity) demonstrate a more or less constant behaviour.
The fracture toughness demonstrates a constant value for a large temperature range, but at the glass transition temperature this property markedly increases. These temperature-dependent properties are key factors in understanding the thermal behaviour of glass elements and are indispensable in numerical models. However, more experiments should be conducted to better understand the scatter in the results and to determine the parameters in temperature ranges that correspond to fire loading.
Concerning the experimental research outcomes of monolithic glass elements, some general findings could be derived. The three most important influencing parameters out of the numerous influencing parameters are the fire location (i.e. the exposure), the kind of glass element and the installation form. Configuration-specific guidance has been presented, but these cannot readily be extrapolated to other situations. Next to that, the fire performance of fully toughened glass is found to be greater than the fire performance of clear float glass.
By contrast, processed glass such as coated and grounded glass demonstrates a smaller fire performance compared to clear float glass due to a larger amount of surface flaws decreasing the glass breakage strength. For frame-supported glass, the semi-exposed frame, more specifically the vertically-hidden frame, demonstrates a betterfire performance. For point-supported glass, the fire performance increases when the point-fixings are further away from the centre line. Based on the reported test results, point-supported glass falls out immediately after a crack initiates at a point support.
The experimental research outcomes of layered glass products highlight different points of attention. Due to the presence of an extra glass pane, the fire performance of both laminated glass and double glazing is larger than the fire performance of clear single glass. Comparing the laminated glass with the double glazing, the latter is reported to have the best fire performance because the thermal resistance of air is larger than the thermal resistance of interlayer material. Gas bubbles appear in the PVB interlayer and SG interlayer of laminated glass when a temperature of respectively 90°C and 150°C is reached at the interlayer.
In case of structural glass beams, which are subjected to both thermal and mechanical loading, a continuous laminate performs better than a discontinuous (i.e. segmented) laminate. Local debonding of the segments causes the beam to fail by buckling. Glass beams made of AN glass layers prove to heat up faster than glass beams of both HS and TT glass layers. Consequently, AN glass beams tend to break first. Concerning the Timber-Glass composite beam, the fire performance is lower compared to the fire performance of the glass web itself. The shading originating from the opaque flanges causes large thermal gradients resulting in early failure of the glass web.
The general findings of monolithic glass and the layered glass products however have limitations. Since the outcomes are based on a specific setup and loading configuration, additional tests should be performed if information is needed about these parameters in another setup or loading configuration. If additional tests have to be performed each time the setup changes compared to the setup fromthe performed studies, a lot of time and money would be spentto these tests. A solution to this problem could be the adoption of advanced finite element modelling.
However, the numerical modelling of the behaviour of glass exposed to fire is still in early stages. Some developed models are presented in this paper and even when these models demonstrate a dynamic stress distribution in good agreement with the reality, it still has its limitations. Crack propagation can be modelled but only one crack path can be calculated while in reality several crack paths appear when a glass element is subjected to thermal loading.
From this paper, it can be concluded that the field of fire resistance of glass elements still needs additional research. Describing the temperature-dependent properties over the entire fire temperature range, performing more experiments to better understand the scatter of the mentioned properties and enhancing the numerical models such that they correspond more to the reality are some research areas which require further research focus.
8. References
Babrauskas, V.: Glass breakage in fires. Fire Sci. Technol (2011)
Bach, H.: Low Thermal Expansion Glass Ceramics. Berlin (2013). doi:10.1007/978-3-662-03083-7
Bedon, C.: Structural Glass Systems under Fire: Overview of Design Issues, Experimental Research, and Developments. Adv. Civ. Eng.(2017). doi:10.1155/2017/2120570
Bedon, C., Zhang, X., Santos, F., Honfi, D., Kozłowski, M., Arrigoni, M., Figuli, L., Lange, D.: Performance of structural glass facades under extreme loads –Design methods, existing research, current issues and trends. Constr.Build.Mater.(2018a). doi:10.1016/j.conbuildmat.2017.12.153
Bokel, R. M. J.,Veer, F. A., Tuisinga,L.:Fire resistance of glass. Proceedings of Glass Processing Days 2003, 362-363 (2003)
Choi, Y. K., Kim, J. T., Jeong, M. G., Cho, S. W., Ryou, H. S.: The influence of fire size on breakage time for double glazed curtain wall system in enclosure fire. J. Mech. Sci. Technol.32(2), 977–983(2018). doi:10.1007/s12206-018-0148-7
Debuyser, M.: Exploratory Investigation of the Behaviour of Structural Glass in Fire. Master’s Thesis, Ghent University. Faculty of Engineering and Architecture, Ghent, Belgium(2015)
Debuyser, M., Sjöström, J., Lange, D., Honfi, D., Sonck, D., Belis, J.: Behaviour of monolithic and laminated glass exposed to radiant heating. Constr. Build. Mater.130, 212–229(2017). doi:10.1016/j.conbuildmat.2016.09.139
Dembele, S., Rosario, R. A. F., Wen, J. X.: Thermal breakage of window glass in room fires conditions –Analysis of some important parameters. Build. Environ.54, 61–70(2012). doi:10.1016/j.buildenv.2012.01.009
EN13501-2: Fire classification of construction products and building elements -Part 2: Classification using data from fire resistance tests, excluding ventilation services(2016)
EN1363-1: Fire resistance tests -Part 1: General Requirements(2012)
Feldmann, M., Kasper, R.: Guidance for European Structural Design of Glass Components. Brussels, Belgium(2014). doi:10.2788/5523
Foraboschi, P.: Analytical modeling to predict thermal shock failure and maximum temperature gradients of a glass panel. Mater. Des.134, 301–319(2017). doi:10.1016/j.matdes.2017.08.021
Haldimann, M., Luible, A., Overend, M.: Structural use of glass. Zurich, Switzerland: International Association for Bridge and Structural Engineering (IABSE) (2008)
Harada, K., Enomoto, A., Uede, K., Wakamatsu, T.: An Experimental Study On Glass Cracking And Fallout By Radiant Heat Exposure. Fire Saf. Sci. 6, 1063–1074(2000). doi:10.3801/IAFSS.FSS.6-1063
Hu, W.C., Nurcholik, S. D., Lee, S.K., Lin, T.H.: Evaluations on heat resistance of curtains with water film in a fire. J. Chinese Inst. Eng.39(5), 615–622(2016). doi:10.1080/02533839.2016.1146092
Kerper, M. J., Scuderi, T. G.:Mechanical Properties of Chemically Strengthened Glasses at High Temperatures. J. Am. Ceram. Soc.49(11), 613–618(1966). doi:10.1111/j.1151-2916.1966.tb13179.x
Klassen, M. S., Sutula, J. A., Holton, M. M., Roby, R. J., Izbicki, T.: Transmission through and breakage of multi-pane glazing due to radiant exposure. Fire Technol.42(2), 79–107(2006).doi:10.1007/s10694-006-7254-x
Kozłowski, M., Bedon, C., Honfi, D.:Numerical Analysis and 1D/2D Sensitivity Study for Monolithic and Laminated Structural Glass Elements under Thermal Exposure. Materials (Basel)11(8), 1447(2018). doi:10.3390/ma11081447
Le Bourhis, E., Rouxel, T.:Indentation response of glass with temperature. J. Non. Cryst. Solids316(1), 153–159(2003).doi:10.1016/S0022-3093(02)01948-8
Louter, C., Nussbaumer, A.: Fire Testing of Structural Glass Beams; Initial Experimental Results. Proceedings of the GlassCon Global Conference -Boston -(2016)
Lu, W., Chen, H., Wang, Y., Duan, Q., Jiang, L., Wang, Q., Sun, J.: Study of point-supported glass breakage behavior with varying point-covered areas under thermal loading. International Journal of Thermal Sciences 132, 65–75(2018a). doi:10.1016/j.ijthermalsci.2018.05.045
Lu, W., Duan, Q., Chen, H., Li, H., Liu, Y., Wang, Q., Sun, J.:Thermal response and resistance optimization of various types of point-supported glass facades. Constr. Build. Mater.(2019). doi:10.1016/j.conbuildmat.2019.07.032
Lu, W., Wang, Y., Chen, H., Jiang, L., Duan, Q., Li, M., Wang, Q.,Sun, J.: Investigation of the thermal response and breakage mechanism of point-supported glass facade under wind load. Int. J. Therm. Sci.132, 65–75(2018b). doi:10.1016/j.conbuildmat.2018.07.114
Malou, Z., Hamidouche, M., Bouaouadja, N., Chevalier, J., Fantozzi, G.:Thermal shock resistance of a soda lime glass. Ceram. -Silikaty57(1),39–44(2013)
Manzello, S. L., Gann, R. G.,Kukuck, S. R., Prasad, K. R., Jones, W. W.: An experimental determination of a real fire performance of a non-load bearing glass wall assembly. Fire Technol. 43(1), 77–89(2007). doi:10.1007/s10694-006-0001-5
New Glass Technology: Brandwerend Glas. https://www.newglasstech.com/?page=product&cat=Safety&product=brandwerend-glas&lang=nl(2020). Accessed on 6 January 2020
Rouxel, T.:Elastic Properties and Short-to Medium-Range Order in Glasses. J. Am. Ceram. Soc.90(10),3019–3039(2007).doi:10.1111/j.1551-2916.2007.01945.x
Rouxel, T., Sanglebœuf, J.-C.:The brittle to ductile transition in a soda–lime–silica glass. J. Non. Cryst. Solids271(3), 224–235(2000). doi:10.1016/S0022-3093(00)00109-5
Shao, G., Wang, Q., Zhao, H., Wang, Y., Sun, J., He, L.:Thermal Breakage of Tempered Glass Façade with Down-Flowing Water Film Under Different Heating Rates. Fire Technol.52(2), 563–580(2016). doi:10.1007/s10694-015-0499-5
Shen, J., Green, D. J., Tressler, R. E., Shelleman, D. L.:Stress relaxation of a soda lime silicate glass below the glass transition temperature. J. Non. Cryst. Solids324(3), 277–288(2003). doi:10.1016/S0022-3093(03)00260-6
Shields, T. J., Silcock, G. W., Flood, F.:Behaviour of Double Glazing in Corner Fires. Fire Technol.41, 37–65(2005)
Shields, T. J., Silcock, G. W. H., Flood, M.:Performance of a single glazing assembly exposed to a fire in the centre of an enclosure. Fire Mater., 26(2), 51–75(2002). doi:10.1002/fam.783
Shields, T. J., Silcock, G. W. H., Flood, M. F.:Performance of asingle glazing assembly exposed to enclosure corner fires of increasing severity. Fire Mater.25(4), 123–152(2001). doi:10.1002/fam.764
Sjöström, J., Kozlowski, M., Honfi, D., Lange, D., Albrektsson, J., Lenk, P., Eriksson, J.: Fire Resistance Testing ofa Timber-Glass Composite Beam. Int. J. Struct.GlassAdv.Mater. Res.4, 24-40 (2020). doi: 10.3844/sgamrsp.2020.24.40
Sjostrom, J., Lange, D., Debuyser, M., Honfi, D., Sonck, D., Belis, J.:Application of Concepts of Fire Resistance of Load Bearing Structural Glass. 9th Int. Conf. Struct. Fire, (April 2018), 869–876(2016)
Skelly, M. J., Roby, R. J., Beyler, C. L.:Experimental investigation of glass breakage in compartment fires. J. Fire Prot. Eng.3(1), 25–34(1991). doi:10.1177/104239159100300103
Tsao, J. Y.:Two semiempirical expressions for condensed-phase heat capacitiesJ. Appl. Phys.68(4), 1928–1930(1990).doi:10.1063/1.346588
Vandebroek, M.: Thermal fracture of glass.Doctoral dissertation. Ghent University. Faculty of Engineering and Architecture, Ghent, Belgium (2014)
Van Der Tempel, L.: Thermal Conductivity of a Glass : The Empirical Model. Glas. Phys. Chem.28(3), 147–152(2002)
Veer, F. A., van der Voorden, M., Rijgersberg, H.,Zuidema,J.:Using transparent intumescent coatings to increase the fire resistance of glass and glass laminates.Proceedings of Glass Processing Days 2001–Tampere, Finland –392–396, (2001).
Wang, Q., Chen, H., Wang, Y., Wen, J. X., Dembele, S., Sun, J., He, L.: Development of a dynamic model for crack propagation in glazing system under thermal loading. Fire Saf. J. 63, 113–124(2014g). doi:10.1016/j.firesaf.2013.11.003
Wang, Q., Wang, Y., Chen, H., Xiao, H., Sun, J., He, L.:Frame constraint effect on the window glass crack behavior exposed to a fire. Eng. Fract. Mech.108, 109–119(2013). doi:10.1016/j.engfracmech.2013.03.010
Wang, Q., Wang, Y., Zhang, Y., Chen, H., Sun, J., He, L.:A stochastic analysis of glass crack initiation under thermal loading. Appl. Therm. Eng. 67(1–2), 447–457(2014c). doi:10.1016/j.applthermaleng.2014.01.075
Wang, Q., Zhang, Y., Wang, Y., Sun, J., He, L.: Dynamic three-dimensional stress prediction of window glass under thermal loading. Int. J. Therm. Sci.59, 152–160(2012). doi:10.1016/j.ijthermalsci.2012.03.018
Wang, X., Tan, Q., Wang, Z., Kong, X., Cong, H.:Preliminary study on fire protection of window glass by water mist curtain. Int. J. Therm. Sci.125, 44–51(2018a). doi:10.1016/j.ijthermalsci.2017.11.013
Wang, Y.:Experimental and Numerical Study of Glass Façade Breakage Behavior under Fire Conditions(2019). doi:10.1007/978-981-13-6484-6
Wang, Y.:The Breakage Behavior of Different Types of Glazing in a Fire. The Proceedings of 11th Asia-Oceania Symposium on Fire Science and Technology,549–560(2020).doi:10.1007/978-981-32-9139-3_40
Wang, Y., Li, K., Su, Y., Lu, W., Wang, Q., Sun, J., He, L.,Liew, K. M.: Determination of critical breakage conditions for double glazing in fire. Appl. Therm. Eng.111, 20–29(2017a).doi:10.1016/j.applthermaleng.2016.09.079
Wang, Y., Wang, Q., Shao, G., Chen, H., Su, Y., Sun, J., He, L., Wen, J., Zong, R.,Liew, K.:Experimental Study on Thermal Breakage of Four-Point Fixed Glass Façade. Fire Safety Science 11, 666–676(2014d). doi:10.3801/IAFSS.FSS.11-666
Wang, Y., Wang, Q., Shao, G., Chen, H., Su, Y., Sun, J., He, L.,Liew, K. M.:Fracture behavior of a four-point fixed glass curtain wall under fire conditions. Fire Saf. J. 67, 24–34 (2014f). doi:10.1016/j.firesaf.2014.05.002
Wang, Y., Wang, Q., Shao, G., Chen, H., Sun, J., He, L., Liew, K. M.:Experimental study on critical breaking stress of float glass under elevated temperature. Mater. Des.60, 41–49(2014a).doi:10.1016/j.matdes.2014.03.038
Wang, Y., Wang, Q., Su, Y., Sun, J., He, L., Liew, K. M.:Experimental study on fire response of double glazed panels in curtain walls. Fire Saf. J.92, 53–63(2017b). doi:10.1016/j.firesaf.2017.05.016
Wang, Y., Wang, Q., Su, Y., Sun, J., He, L., Liew, K. M.:Fracture behavior of framing coated glass curtain walls under fire conditions. Fire Saf. J. 75, 45–58(2015). doi:10.1016/j.firesaf.2015.05.002
Wang, Y., Wang, Q., Sun, J., He, L., Liew, K. M.:Effects of fixing point positions on thermal response of four point-supported glass façades. Constr. Build. Mater.73, 235–246(2014b).doi:10.1016/j.conbuildmat.2014.09.085
Wang, Y., Wang, Q., Sun, J., He, L., Liew, K. M.:Thermalperformance of exposed framing glass façades in fire. Mater. Struct. 49(7), 2961–2970(2016). doi:10.1617/s11527-015-0698-z
Wang, Y., Wang, Q., Wen, J. X., Sun, J., Liew, K. M.:Investigation of thermal breakage and heat transfer in single, insulated and laminated glazing under fire conditions. Appl. Therm. Eng.125, 662–672(2017c). doi:10.1016/j.applthermaleng.2017.07.019
Wang, Y., Wu, Y., Wang, Q., Liew, K. M., Chen, H., Sun, J., He, L.:Numerical study on fire response of glass facades in different installation forms. Constr. Build. Mater. 61, 172–180 (2014e). doi:10.1016/j.conbuildmat.2014.03.012
Wang, Y., Xie, Q., Zhang, Y., Wang, Q., Sun, J.:Sensitivity analysis of influencing factors on glass façade breakage in fire. Fire Saf. J.98, 38–47(2018b).doi:10.1016/j.firesaf.2018.04.002
Xie, Q., Zhang, H., Si, D.:Experimental study on critical breakage stress of float glass with different thicknesses under conditions with temperatures of 25 and 200°C. Fire Mater.35(5), 275–283(2011). doi:10.1002/fam.1052
Yang, Z., Zhao, X., Wu, X., Li, H.L.: Application and Integrity Evaluation of Monolithic Fire-resistant Glass. Procedia Eng.11(5), 603–607(2011). doi:10.1016/j.proeng.2011.04.702