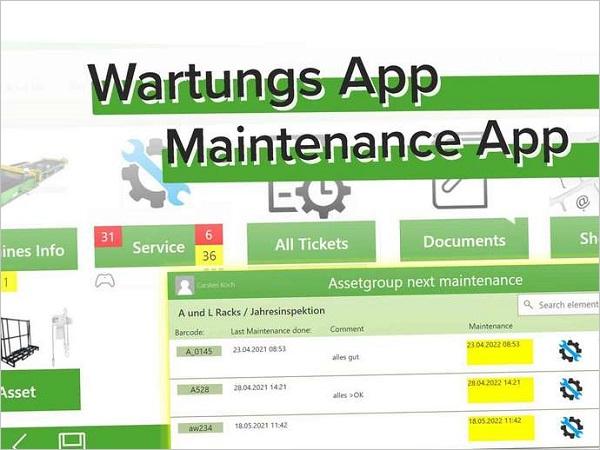
Date: 12 April 2022
Gone are the lists and memos for organizing maintenance and service
From servicing machines and air conditioning systems to inspections of measuring equipment, there are a lot of tasks for employees to bear in mind and carry out. And while the list might look short and easy when written on a quick memo or an Excel spreadsheet, they often come with little difficulties and niggles for the staff to resolve. Sometimes the necessary maintenance records will be missing, or the might end up being pushed back, resulting in a tighter turnaround and more pressure for the employees. Some may also feel that repetitive routine checks are a burden, unnecessary or even a waste of time. HEGLA New Technology’s Shop-Floor Assistant is a new app with a special maintenance functionality that makes organising and carrying out maintenance easier.
“The productivity of any production department depends on the efficiency of its machines and the production time available,” explains Managing Director Markus Schoisswohl of HEGLA New Technology. “That’s why creating a well-organised maintenance system that would enable teams to prevent downtime and maintain performance was one of our most important goals when developing the app.”
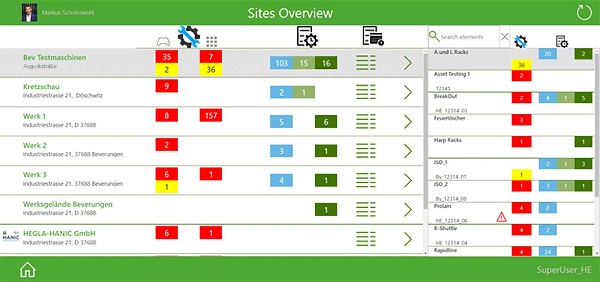
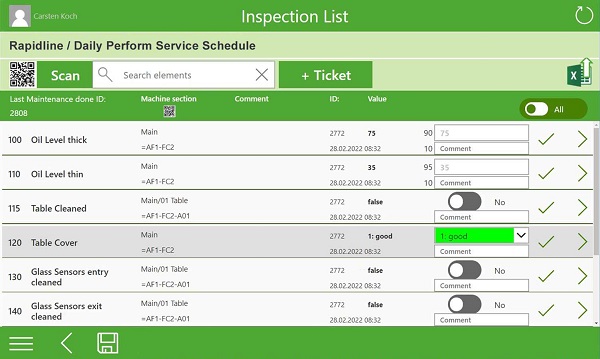
Technological progress leads to changes in maintenance requirements
Technological progress has boosted performance significantly in glass processing companies, while also leading to changes in maintenance requirements. On any given day, there are sensors to be checked, containers to be emptied and production resources to be refilled. In addition to this, annual maintenance is required for production resources such as racks and chain hoists, while designated wear parts need to be replaced at specific intervals. “The more machines a company has, the harder it is to keep track of things – especially if the team in question is responsible not only for production, but for all the technology as well,” Dr Schoisswohl says. “There’s a lot of different tasks to carry out, so everything needs to be organised and you need a clear idea of who’s in charge of what.”
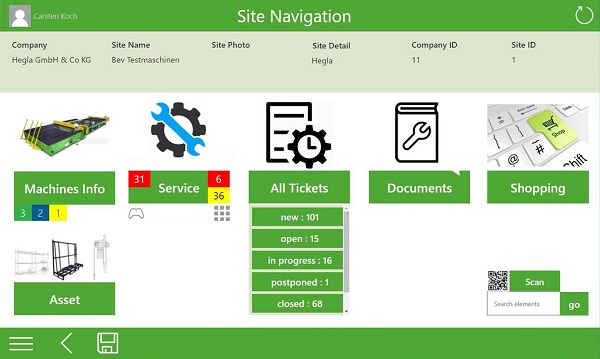
All your technical systems in one app
The app’s maintenance area keeps a centralised record of all the company’s technical systems and machines, along with their respective maintenance intervals. As soon as it is activated, the app will start sending individual employees, the whole team, or the supervisor alerts for upcoming deadlines and work as required. In addition to this, documentation, maintenance instructions, spare parts lists and all other papers, data and sketches can be stored in the app cloud so that all the users can stay up to date on the current status, no matter where they are. “Experience has shown us that searching for the required manufacturer’s instructions and spare parts lists regularly leads to unplanned interruptions and frustration on the part of staff,” said the Managing Director. It is also possible to store a list of the required wear parts for each maintenance activity to ensure that they are supplied on time when someone orders or reserves them in the app.
The app also features a ticket function. This allows users to set the various tasks can be set at any time and assign them to an in-house technician for completion – be it spontaneously on the shop floor or later in the office. Photos can also be added to the tick to provide more clarity and document the work. The structuring app system offers advantages for almost every production or administration employee Users can forward requests for maintenance or support straight away without knowing exactly who they need to speak to – an elegant way of ensuring that no one forgets what needs doing.

Organised completion process with proof of work
In the app, team leads can see which maintenance tasks and tickets have been completed and which are still being processed. This makes it possible to track the sequence in which activities have been carried out, and the records can also be used as proof of work to show to manufacturers. The records also come with another feature to make investment planning easier: repairs that recur frequently are an indication of vulnerabilities and weaknesses in individual machines. An increasing number of tickets in the log for a particular system provides valuable input for the company’s investment strategy.
“Another of the main advantages the app offers is the ability to store exact records and documentation of mandatory safety inspections in a central location where they can be accessed at any time. It not only provides alerts on upcoming inspections, but also enables employees to present proof at any time,” Dr Schoisswohl adds.
Many of our customers have already placed their trust in the Shop-Floor Assistant, and it is also in use by our colleagues at HEGLA Production Engineering. For Managing Director Andreas Fried of Plattling-based company AGC Interpane, the centralised provision of tickets, deadlines, and maintenance information are major advantages in a cross-manufacturer environment. “Our entire team can now access the documentation for all our technical systems, and they always have a comprehensive overview which tasks are coming up next. It clearly shows what needs to be done, what priority each task has, and what has already been completed,” said Andreas Fried.
The maintenance functionality is part of the Shop-Floor Assistant app from HEGLA New Technology, and can be extended with customer-specific functions such as a digital rack search, scanning for glass identification, or functionality for organising warehouse and logistics departments. The app aims to network the various departments and integrate different manufacturer solutions into a single, independent system.
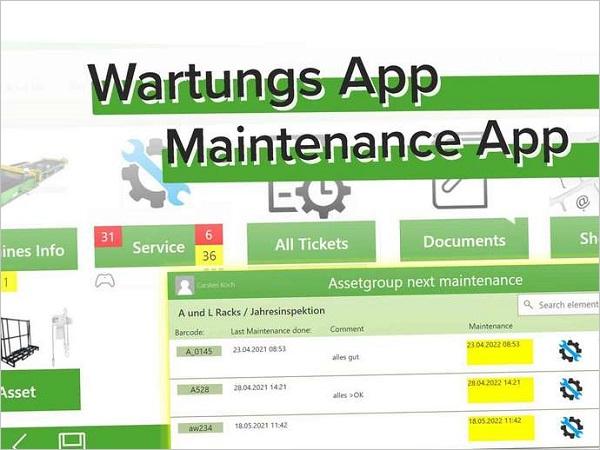

Add new comment